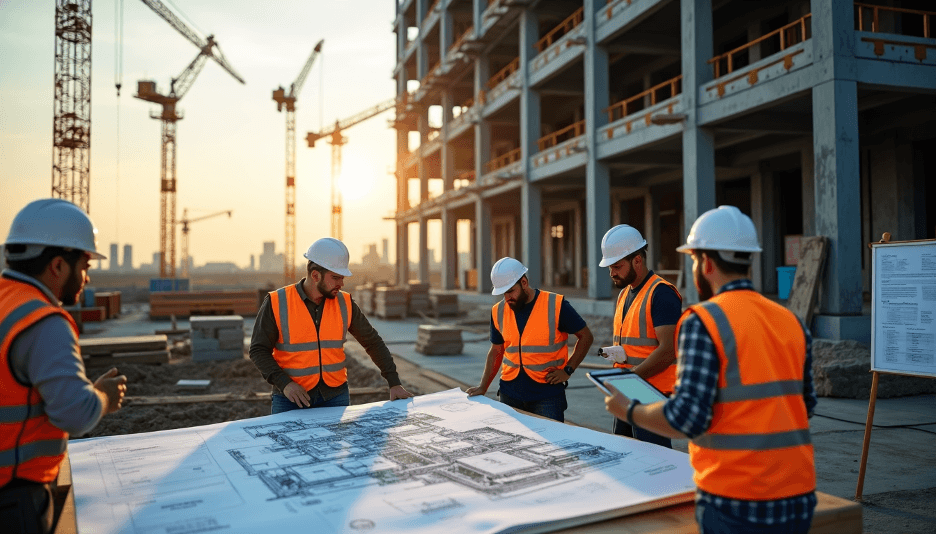
How to Create a Successful Construction Management Plan: A Step-by-Step Guide
A well-laid-out construction management plan builds the foundation of every successful construction project. Managing complex construction projects needs careful coordination of resources, timelines, and stakeholders. Teams can stay on track and deliver projects faster with a complete construction management plan.
This piece walks you through everything you need to develop a construction project management plan that works. You'll learn how to set clear objectives and implement quality control measures. Our straightforward approach covers vital elements like budget planning, timeline development, risk management strategies, and communication frameworks. You can use this practical guide to create a construction management plan template that adapts to projects of all sizes. This ensures consistent success in your construction projects.
Define the Project Scope and Objectives
A clear and complete project scope forms the bedrock of every successful construction project. This significant phase starts when we understand that a project scope outlines all inclusions and exclusions. A well-defined scope helps prevent litigation and establishes clear expectations among all stakeholders.
Identify key stakeholders
Stakeholder identification plays a crucial role in project success. Research shows that only 2.5% of companies complete their projects 100% successfully. Construction projects typically divide stakeholders into two main categories:
- Direct (Internal) Stakeholders: Client, sponsors, project manager and team, consultants, suppliers, and subcontractors
- External Stakeholders: Local residents, government bodies, labor unions, inspecting organizations, and public utilities
Project managers should identify stakeholders early because they are a great way to get expertise about the project. These stakeholders can spot potential constraints that might otherwise go unnoticed.
Establish clear project goals
Project goals need SMART objectives - Specific, Measurable, Achievable, Relevant, and Time-bound. These clear objectives act as our compass that points toward a well-defined destination and helps prevent confusion, delays, and budget overruns.
The project's goals must be specific and measurable. A clear description of performance standards, materials, time requirements, and evaluation criteria for contractors and subcontractors helps maintain focus throughout the project lifecycle.
Outline deliverables and milestones
Project deliverables are the end-results we want to produce. The team must define these results before work begins to keep a clear picture of project completion. Site leadership uses project milestones as key dates or activities that show completed work phases and signal the beginning of new ones.
A work breakdown structure (WBS) helps us split each deliverable into manageable chunks. This method lets us assign tasks and monitor progress throughout the project. Stakeholders can give feedback on specific parts, which will give a better chance of meeting expectations at each step.
Gantt charts create a visual timeline of project phases that merge deadlines with milestones. Team members can see how their contributions fit into the bigger picture and understand why staying on schedule matters.
Develop a Comprehensive Project Schedule
Creating a detailed project schedule plays a significant role to maintain control over construction timelines and resources. A well-laid-out schedule acts as our roadmap through the project lifecycle and ensures proper coordination to complete all tasks on time.
Create a work breakdown structure
A Work Breakdown Structure (WBS) visually represents all the work to be done to complete the project. This proven approach helps teams break down complex projects into three main types:
- Deliverable-based WBS: Focuses on tangible project outputs
- Phase-based WBS: Organizes tasks by project stages
- Activity-based WBS: Breaks down work into specific activities
The WBS captures the project's full scope and identifies major deliverables. This comprehensive approach prevents scope gaps and helps teams avoid schedule delays and additional costs.
Estimate task durations
Task duration estimates rely on bottom-up estimating techniques that determine realistic timelines. A construction schedule helps builders control costs by aligning material deliveries with subcontractors. Project managers must think over these key factors for duration estimates:
- Historical data from similar projects
- Expert judgment from experienced team members
- Resource availability and constraints
- Buffer time between phases
Our team's experience shows that discussions about previous jobs with team members and experienced contractors lead to realistic timing. This shared planning approach will give us practical and achievable estimates.
Identify critical path and dependencies
The Critical Path Method (CPM) stands as the most common scheduling technique in construction. Our team implements CPM to identify the longest stretch of dependent activities. This method helps measure completion time from start to finish.
Project timelines depend heavily on task dependencies that can substantially affect progress. Task B depends on task A when we need to complete task A first. CPM enables us to create a project network that delivers these benefits:
- A planning schedule for the entire construction team
- A solid foundation to track project performance
- A way to measure actual progress against planned progress
Our team updates the network diagram with new information regularly. This approach provides schedule flexibility instead of relying on early estimates alone. The project stays on track while adapting to changes effectively.
Establish a Robust Budget and Cost Control System
Cost control plays a significant role in construction project management. The numbers tell a compelling story - 75% of projects exceed their original budget by a lot. Construction companies need reliable budget control systems because only 25% of projects stay within 10% of their original budget.
Estimate project costs
Project budgeting starts with a complete cost estimation. Contractors paid USD 97.00 billion more than expected in materials and labor costs in 2023. We analyze all expenses to get the full picture of what it all means:
- Direct costs (labor, materials, equipment)
- Indirect costs (overhead, permits, administrative)
- Subcontractor fees
- Insurance and bonds
- Regulatory compliance costs
Set up cost tracking mechanisms
Our team sets up dedicated systems that track expenses throughout the project lifecycle. A dedicated person must oversee cost tracking to ensure the project's financial health. This professional maintains complete oversight of:
- Progress updates and invoices
- Purchase orders and material costs
- Labor productivity metrics
- Equipment utilization rates
- Change order documentation
Construction management software helps us deliver up-to-the-minute data on labor productivity and costs. The technology spots potential delays or budget overruns early and allows swift corrective action.
Plan for contingencies
Our construction management plan sets aside 5-10% of the total budget for contingencies. This financial buffer protects us against unexpected challenges like:
- Material price fluctuations
- Weather-related delays
- Unforeseen site conditions
- Regulatory changes
- Subcontractor issues
We base our contingency planning on a full picture of potential risks. This strategy helps us avoid expensive last-minute fixes. Our strong cost control measures create a financial structure that delivers successful projects and keeps them profitable.
We track and update our cost forecasts regularly. This lets us offset higher costs in some areas by cutting back in others. Our stakeholders receive regular cost reports that keep them updated about the project's financial health and budget progress.
Create a Risk Management Strategy
Our construction management plan puts risk management at the heart of project success. Years of experience have taught us that construction projects need proactive risk identification and management. This approach demands careful planning and systematic execution to shield projects from delays and setbacks.
Identify potential risks
Risk management starts during the pre-construction phase. Early identification helps us address challenges right away. Our detailed approach covers:
- Financial and Economic Risks
- Physical and Safety Risks
- Design and Technical Risks
- Construction-Related Risks
- Political and Environmental Risks
- Acts of God Risks
Project teams and stakeholders participate in regular brainstorming sessions that utilize their expertise and different views. Their shared approach reveals risks that might not be obvious from a single view and ensures we capture both clear and subtle challenges.
Assess risk impact and probability
Once we spot risks, we use a 5×5 risk assessment matrix to evaluate them. The evaluation looks at two key factors:
- Probability Scale (1-5):
- Very Unlikely (1): Rarely happens
- Possible (3): Could go either way
- Very Likely (5): Almost bound to happen
- Impact Scale (1-5):
- Negligible (1): Barely affects the project
- Moderate (3): Takes real effort to fix
- Catastrophic (5): Could make the project fail
We get the risk rating when we multiply how likely it is by its effect. This helps us decide which risks need attention first. The approach lets us put our resources where they matter most.
Develop risk mitigation plans
Our team creates targeted solutions for each risk we spot. The strategy has four main ways to handle risks:
Risk Reduction: We put preventive measures and better controls in place for risks we can minimize. Our team might invest in additional safety training to cut down workplace incidents.
Risk Transfer: Some risks work better when moved to other parties through insurance or contracts. This works well when we make subcontractors take charge of specific risk areas.
Risk Avoidance: High-impact risks often need project changes that remove the risk completely. We might change design elements or move certain project parts to different locations.
Risk Acceptance: Some risks stay with us when we can't eliminate or transfer them. We plan ahead and set resources aside to handle what might come up. Good planning and smart budget choices help us deal with possible problems.
Our team keeps an eye on risks as the project moves forward. New risks can pop up anytime. Quick team meetings and updates with stakeholders help us stay ahead of issues. This flexible approach lets us adjust our response as things change and keeps the project running smoothly.
Design an Effective Communication Plan
Strong communication strategies make construction projects work smoothly. Our experience reveals that miscommunication in construction can lead to project delays, higher turnover rates, and extra costs. Clear communication channels aid information exchange between stakeholders and are the key to project success.
Determine communication channels
The project needs multiple communication channels that let information flow smoothly. We pick the best methods based on message types and urgency. Our main channels are:
- Project management software and digital tools
- Face-to-face meetings and site visits
- Email updates and document sharing
- Mobile apps for live updates
- Cloud platforms for central information access
The team should define their preferred communication methods clearly. Response times must be specified for different types of messages. This well-laid-out system will prevent gaps in information and speed up decision-making.
Set up reporting structures
A clear reporting hierarchy helps maintain smooth communication flow. Research shows that establishing a formal communication chain helps team members understand their reporting lines and know whom to ask questions. The team's reporting structure needs these key steps:
- Document the chain of command as specified in construction contracts
- Establish regular progress meeting schedules
- Implement standardized reporting templates
- Set up document control systems
- Define version control protocols
Construction management tools streamline communication by putting project information in one place and providing up-to-the-minute updates. This approach will give all stakeholders access to current project documentation and updates.
Plan for stakeholder engagement
Our stakeholder engagement strategy encourages two-way communication and active participation. Research shows that effective communication with stakeholders involves listening, explaining, exchanging knowledge, and solving problems with patience. Here's how we do it:
Regular Progress Meetings: Weekly or bi-weekly meetings provide a dedicated platform for stakeholders to discuss project updates and address concerns. These meetings make open communication and shared problem-solving easier.
Feedback Mechanisms: Clear processes help stakeholders provide input and raise concerns. This proactive approach spots potential issues early and builds positive relationships with everyone involved.
Documentation Protocol: All communication stays properly documented and available to relevant stakeholders. We keep detailed records of meetings, decisions, and action items for future reference and accountability.
Digital Collaboration: We use construction-specific technology to improve our communication. These tools spread information faster and make work easier for all team members.
These communication strategies create an environment where information flows naturally. Our experience proves that good communication improves teamwork, collaboration, quality, and retention. We stay in regular contact with all stakeholders to meet their expectations, deliver quality work, hit deadlines, and control the budget.
Implement Quality Control Measures
Quality control serves as the life-blood of successful project delivery in construction management. Testing and inspecting are essential activities that ensure safety, quality, and compliance throughout the construction process.
Define quality standards
Our first step establishes clear quality requirements that arrange with industry standards and project specifications. A construction quality control system will give a guarantee that deliverables meet the client's standards from day one of the construction process. The acceptance criteria has these key elements:
- Zero visible defects
- Compliance with minimum code standards
- Adherence to manufacturers' specifications
- Conformance to contract requirements
- Project-specific quality standards
- Industry common practices
The standards reference recognized organizations like ASTM, ANSI, ACI, and AWS that provide detailed quality and workmanship specifications. This detailed framework helps us maintain consistency throughout each project phase.
Establish inspection and testing procedures
Quality control relies on our inspection and testing procedures. Products need to be consistent and match their design specifications. Here's our well-laid-out approach to inspections:
- Design clear inspection plans before construction starts
- Create complete checklists to verify quality
- Set up clear documentation methods for inspections
- Schedule regular testing
- Keep detailed records of quality control work
Our experience shows that failure to properly test materials like concrete can weaken structural integrity and create safety risks. We test materials extensively to prevent weak spots in the structure. Steel undergoes strength and hardness testing to validate its properties.
Plan for continuous improvement
We strive to improve our processes through quality control methods that work. Here's how we make it happen:
Kaizen Method: Our team reduces non-conformance costs by finding and fixing the root causes of waste. Every employee plays a role in this process. This method helps us keep quality high while making the best use of our resources.
PDCA Cycle: This total quality management system helps us build quality products and keeps our customers happy. The cycle stops mistakes from happening again and keeps communication flowing between all workforce levels.
Data-Driven Analysis: Our construction quality management software boosts quality control through automation, accessibility, and visibility. The technology lets us:
- Track deficiencies step by step
- Record corrections and verifications
- Spot trends to improve processes
- Give live quality updates
Quality control must be everyone's priority on the project team. We've learned that quality improvement done right leads to better productivity. It suggests new ways to work and prevents do-overs.
Our zero-defect policy stays strong through regular checks during construction. We inspect thoroughly, collect data, track issues, and listen to feedback. Our quality control process stays clear by:
Pre-construction Planning: Each project gets its own quality control plan based on specific details instead of generic solutions.
Implementation Phase: We team up with inspection agencies and get design team reviews early.
Verification Process: We build mock-ups and compare samples to match our quality standards.
This complete approach to quality control will give our construction management plan reliable, top-quality results. These measures help avoid pricey repairs, check structural integrity, and confirm all construction elements meet required codes.
Conclusion
Construction project management succeeds when six key parts work together: scope definition, schedule development, budget control, risk management, communication planning, and quality control. These elements form a detailed system where each part strengthens the others. A clear project scope shapes the schedule naturally. The project's cost controls back up risk management plans effectively. Quality standards stay high when teams communicate well during the work.
Construction teams that use this approach set their projects up to win. They organize better, face fewer risks, and keep stakeholders happy. Project teams get clear direction and use resources wisely. They run into fewer surprises as work moves forward. This well-laid-out method helps teams deliver great results in construction projects of all sizes. Teams meet their goals and maintain high quality standards consistently.
FAQs
What is included in a construction management plan?
A construction management plan typically encompasses the scope of the project, design and budget details, resource allocation and task assignments, team and personnel involvement, project identification and description, plan outlining, feedback incorporation, and final plan approval.
What are the key steps to develop a management plan?
The five essential steps to create a management plan are: defining your objectives, determining the project scope, preparing a detailed schedule, implementing quality assurance measures, and continuously monitoring and tracking project progress. Tools like Kanban boards, Scrum boards, and Gantt charts are often used to facilitate these steps.
How can you write an effective project management plan?
To write an effective project management plan, start by establishing the project scope and metrics. Identify key stakeholders and outline the project deliverables. Develop actionable tasks and assign them with specific deadlines. Share the plan, gather feedback, and make necessary adjustments to the project plan as needed.
How do you develop a construction plan?
Developing a construction plan involves defining the project scope and budget, obtaining planning permission, creating a detailed project schedule, conducting a risk assessment, assigning a project manager, assembling your team, executing the construction phase plan, and measuring project progress to make any necessary adjustments.
Latest articles
Trusted by global leaders
Join those who have put their trust in us