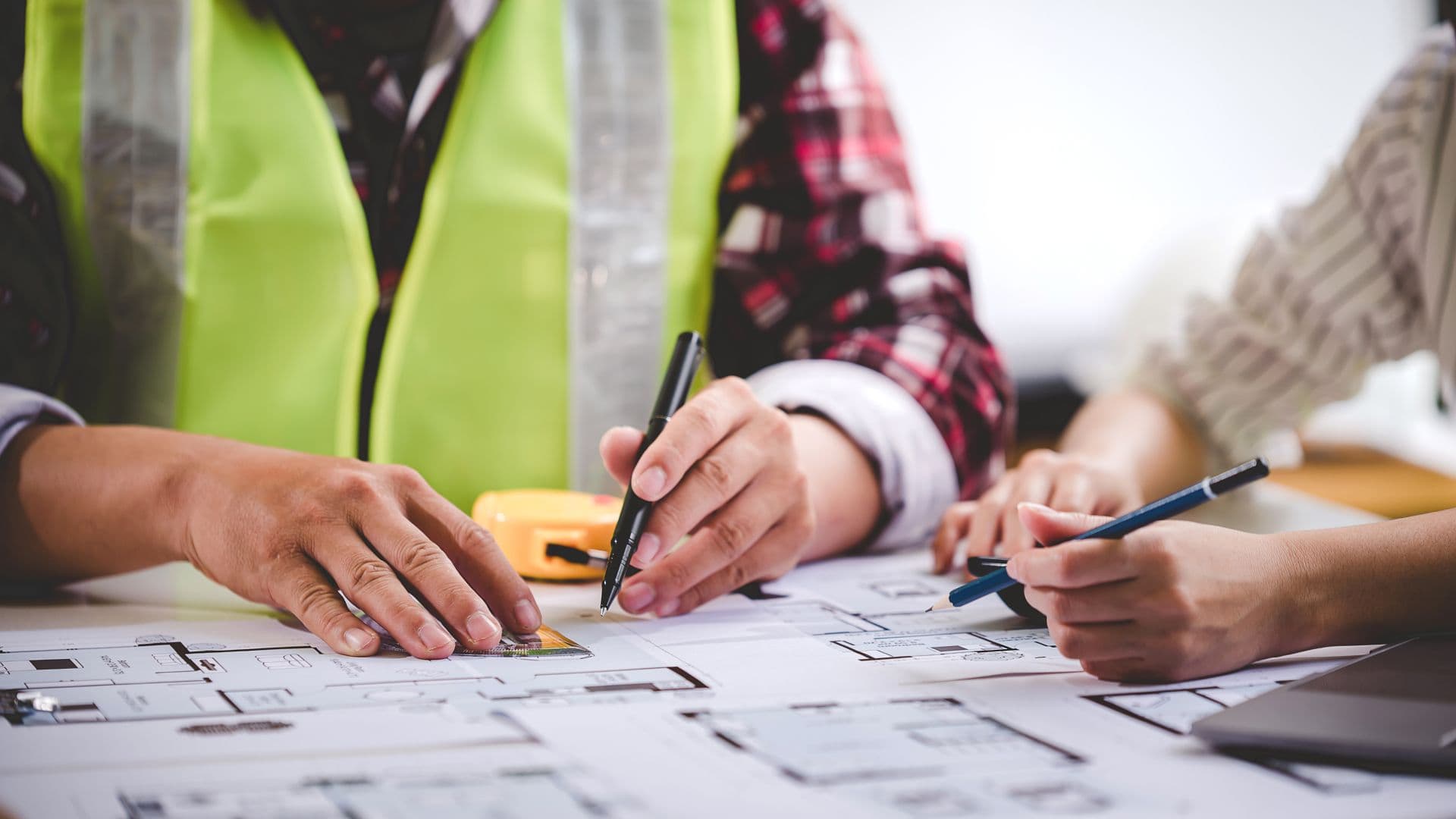
Shop Drawings vs Construction Drawings: Real Differences Explained
Construction projects depend on two different types of drawings that create confusion among industry professionals. Shop drawings and construction drawings play unique roles at different stages of the building process. Architects create construction drawings to show the overall design, and contractors develop shop drawings that detail specific components for fabrication and installation. Building Information Modeling (BIM) has made both drawing types more accurate and helps reduce errors in modern construction projects. The difference between these drawings is significant to project success. This piece explains everything in shop drawings and construction drawings that helps professionals make informed decisions throughout the construction process.
Basic Differences Between Shop and Construction Drawings
The biggest differences between shop drawings and construction drawings show up in how they're created, their timing, and their main goals. These differences guide construction projects from initial concept to final completion.
Who Makes Each Type
Property owners ask architects and engineers to create construction drawings at the property owner's request. These professionals handle the building's overall design and structural elements. Shop drawings come from contractors, subcontractors, manufacturers, or suppliers after they sign the construction contract. Premier Construction Software's drawing management system tracks these drawing types and their creators throughout the project.
When They're Created
Teams develop construction drawings during the pre-construction phase as the design takes shape. These drawings are the foundations for project planning and bidding processes. Shop drawings follow later during the construction phase. They give fabricators detailed information about manufacturing components and installation needs.
Main Purpose of Each Drawing Type
Construction drawings show the project's complete vision. They detail structural use, features, appearance, estimated dimensions, and equipment performance. They also help contractors estimate labor, materials, and construction costs during bidding.
Shop drawings translate the design intent and field conditions into reality. They include complete framing specifications and show how specific construction components fit together and get installed. Each subcontractor submits their own shop drawings that need approval. These focus on specific elements like:
- Beams and trusses
- Equipment layouts
- Mechanical systems
- Electrical components
Shop drawings ensure precise coordination between different construction elements. These detailed plans turn the architect's vision into useful instructions for fabricators and installers. This makes shop drawings essential links between design concepts and real-world implementation.
What are Construction Drawings?
Technical documents are the foundations of construction drawings that serve as a universal language between designers, engineers, and contractors. These drawings show every detail of a building project, from floor plans to structural specifications.
Key Components
Construction drawings have several vital elements that come together to show the complete building design. Architects and engineers include:
- Floor plans and elevations that show spatial layouts
- Structural drawings with load-bearing elements
- MEP (Mechanical, Electrical, Plumbing) system layouts
- Site plans that show landscape integration
- Detailed specifications for materials and methods
Premier Construction Software's drawing management system organizes these components in a systematic way. Teams can track changes and keep version control throughout the project lifecycle.
Design Intent Focus
Construction drawings show the architect's vision and technical requirements. They set basic criteria that guide the development of detailed engineering documents. Engineers and contractors will build upon these design criteria in later phases.
These drawings have many critical roles. They act as contract documents between project stakeholders. On top of that, they help get necessary permits by showing compliance with local building codes and safety standards.
Architects use standardized symbols and markings to create these drawings, which results in a universal technical language. Each element follows graphic standards and conventions that are 50 years old, especially when you have to construct drawing sets.
Construction drawings are different from conceptual sketches. They contain exact measurements, material specifications, and detailed notes that guide the construction team. These documents work among other written specifications and detail all materials, techniques, and standards needed to complete the project.
The drawings combine input from experts of all types, including structural engineers, HVAC specialists, and fire safety professionals. This shared approach creates a full picture of the building that allows accurate construction planning and execution.
What are Shop Drawings in Construction?
Shop drawings turn architectural concepts into practical manufacturing instructions. They provide exact details for fabricating and assembling construction components.
Detailed Specifications
Shop drawings hold specific information about dimensions, materials, and assembly methods. Drawing numbers and revision numbers must reference the appropriate design drawings. Premier Construction Software's drawing management system tracks these important specifications throughout the project lifecycle.
These drawings must include:
- Original issue date and revision history
- Project title and address
- Contractor and manufacturer details
- Product and material identifications
- Field dimensions and applicable standards
We focused on prefabricated components such as elevators, structural steel, trusses, precast concrete, windows, and millwork. These documents show how specific elements fit within the overall structure and offer more detail than standard construction drawings.
Installation Guidelines
Installation guidelines are a vital part of shop drawings that outline step-by-step procedures for proper component integration. Welding specifications must show type, size, and weld locations.
Quality control is the foundation of shop drawing development. Contractors must review and approve all shop drawings before submitting them to the registered professional. This process verifies that safety, structural integrity, and functionality are arranged with project requirements.
The drawings point out potential safety risks and installation concerns. Manufacturers often add symbols, data, or specific instructions about component installation, along with lists of required materials like fasteners or adhesives.
Major building systems need third-party reviews. Commercial chillers need evaluation for electrical connections, plumbing, rigging, and insulation compatibility. These reviews confirm that different components work naturally together within the finished structure.
Architects or engineers must approve shop drawings before fabrication starts. This verification process helps prevent errors and confirms that components meet design specifications. Premier's digital platform makes this approval workflow quick and reduces delays in the construction timeline.
Accuracy and Detail Level
Construction and shop drawings have substantially different precision standards that affect project outcomes and quality control. Premier Construction Software's drawing management system tracks these detail levels throughout the project's lifecycle.
Construction Drawing Limitations
Construction drawings by engineers and architects come with inherent constraints. These drawings often contain a degree of ambiguity. Hidden site conditions might mask certain elements, which leads to scaling inaccuracies or missing components in the original plans.
Time constraints force architects to complete their drawings quickly. They focus on design intent rather than detailed specifications. The time pressure results in drawings that show "Verify-in-Field" labels where contractors must check actual dimensions.
Many construction sites still rely on paper-based methods. These methods have weaknesses in cross-referencing and depend heavily on supplementary documents. Such limitations create:
- Design element misinterpretations
- Construction site safety risks
- Execution efficiency problems
- Error-related cost increases
Shop Drawing Precision Requirements
Shop drawings just need rigorous accuracy standards. Contractors perform site investigations to take exact measurements and check clearances. These details help confirm the design and spot potential issues before fabrication starts.
Quality control is the life-blood of shop drawing development. Reviews happen at multiple stages to meet regulatory requirements and industry standards. This process prevents errors and ensures quality across project components.
Shop drawings connect broad architectural plans with actual construction needs. They turn design concepts into practical builder and fabricator instructions. The detailed documentation specifies:
- Component dimensions
- Material requirements
- Assembly steps
- Installation procedures
- Connection specifics
Digital tools have improved drawing accuracy. Coordination between different trades remains challenging. Multiple subcontractors' shop drawings need consistency. Teams hold regular coordination meetings to prevent building system conflicts.
Shop drawing precision supports the final construction phase. Construction changes require documentation through redline markups that become part of as-built drawings. These records prove valuable for future maintenance and modifications.
Drawing Creation Process
You need careful attention to detail and systematic processes to create accurate drawings. Premier Construction Software's drawing management system helps teams work together with digital features.
From Design to Construction Drawings
Architects and engineers create construction drawings through a series of coordinated steps. CAD software has revolutionized the drafting process. It gives users features like layers, templates, and symbol libraries. These digital tools let professionals change and add notes to drawings while they keep the right scale and proportions.
Shop Drawing Development Steps
Shop drawings come together through a well-laid-out approach:
- Review design documents to understand project requirements
- Take field measurements to account for site conditions
- Draft detailed component specifications
- Ask stakeholders for approval
Each step builds on the previous one to create a complete guide for fabrication and installation. We used these drawings to outline manufacturing processes, assembly sequences, and installation methods. Yes, it is important that high-risk projects require shop drawings to arrange everything between all parties.
Quality Control Checks
The core team members start quality control with thorough document reviews. Then drawings go through checks for accurate dimensions, proper cross-referencing, and clear legibility. The review process looks at several critical aspects:
Structural engineers check component specifications. Mechanical and electrical consultants check system compatibility at the same time. This multi-layered review process helps prevent errors and installation conflicts that can get pricey.
Digital platforms optimize quality control. These tools are a great way to get real-time collaboration between project teams. Premier's drawing management system tracks revisions and keeps version control throughout the review cycle.
Teams hold regular coordination meetings to address conflicts between different building systems. Construction drawings must have proper scale and clear annotations to be accurate. Each drawing needs to show physical dimensions correctly and include reference measurements for proper execution.
Legal and Liability Aspects
Legal responsibilities create a clear link between construction and shop drawings. Premier Construction Software's drawing management system tracks these obligations throughout each project's lifecycle.
Construction Drawing Responsibilities
Architects and engineers have specific duties for construction drawings. Standard contracts require design professionals to review submittals that match design concepts. Their review process checks if drawings line up with contract documents rather than proving construction methods or safety measures right.
Contract documents decide which drawings have more authority. Specifications take precedence when differences show up between drawings and specifications. Architects must quickly resolve any discrepancies in figures or specifications through written decisions.
Design professionals risk liability even with limited reviews. The Hyatt Regency Hotel case, now 40 years old, proved architects can't pass on their professional duty to review drawings. Courts have found design professionals liable for negligent shop drawing reviews, especially when you have safety problems.
Shop Drawing Accountability
Contractors hold major responsibility for shop drawing accuracy. Their submissions come with guarantees that they have:
- Reviewed and approved the drawings
- Verified materials and field measurements
- Coordinated information with contract requirements
A contractor's duty goes beyond just submitting drawings. Standard AIA contracts state that contractor approval doesn't free them from contract document requirements. Architect approvals, however, only check if designs line up with concepts.
Legal precedents draw clear accountability boundaries. Courts usually decide that approved shop drawings can't change original contract requirements without written authorization. All the same, contractors must follow approved shop drawings while staying responsible for any contract document changes.
Quality control measures shift how liability gets distributed. Contractors need to review shop drawings before submission. This makes them responsible for accuracy and meeting contract specifications. Premier's digital platform makes this review process quick while creating documentation trails.
The Spearin Doctrine affects who takes responsibility. This legal principle says owners implicitly guarantee their plans and specifications work properly. Contractors can ask for relief if original plan defects cause problems. Courts recognize this doctrine in public and private projects of all sizes.
Final payment doesn't release contractors from their warranty promises. Contract terms often keep claims about work quality alive even after project completion. Architects might face owner liability if their contracts lack specific protection clauses.
Digital Tools and Management
Digital platforms are changing how construction teams manage their drawings. Premier Construction Software's digital solutions make document control easier throughout project phases.
Premier Construction Drawing Software Benefits
Digital construction drawing management software cuts project costs through automated processes. Premier's platform gives teams a central storage space for all project documents and quick access to the latest versions. Teams work faster with:
- Quick drawing sharing
- Automatic version tracking
- Up-to-the-minute updates
- Mobile access
- Easy search options
The software's OCR technology automatically scans and labels sheets. This feature helps drawings load quickly on any device. Teams can access current information without delays or version confusion.
Premier's platform keeps drawings accurate with strict version control. The system tracks every change and creates a clear audit trail. Project managers can see who views updated plans, which keeps everyone accountable during construction.
Digital Collaboration Features
Cloud platforms make coordination between project stakeholders smooth. Teams can share feedback right away using digital markup tools and comment threads. This direct communication cuts down on errors and speeds up decisions.
The platform sends automatic alerts about drawing updates. Field crews get revised plans on their mobile devices immediately. Quick access stops work delays and prevents costly mistakes from old information.
Digital tools help with quality control. Project managers can track drawing reviews and approvals through automated workflows. The system keeps detailed records of all changes, which makes the revision process transparent.
Premier's platform has powerful search features. Teams can find specific drawings quickly through text searches, tags, and filters. This saves valuable time compared to managing documents by hand.
Security features keep sensitive project information safe. The platform lets you control access levels for different team members to keep documents confidential. On top of that, regular backups protect critical project data.
Integration features connect drawings with related documents. Cross-referencing between sheets happens automatically through hyperlinked callouts. This makes it easy to navigate complex drawing sets.
The software's collaboration tools help remote teams work together. Field crews can access drawings from anywhere, which keeps work moving no matter where teams are located. This flexibility helps projects with scattered teams.
Document control features stop unauthorized changes. The system needs proper approvals before any modifications can happen. Teams can keep drawing integrity intact throughout the project.
Digital platforms provide valuable project insights through data analytics. Managers can track how drawings are used and find ways to improve workflows. These measurements help streamline project processes and reduce waste.
Common Drawing Mistakes
Construction projects lose billions each year due to drawing mistakes that cause rework and delays. Premier Construction Software's drawing management system helps teams spot and prevent these errors before they get pricey.
Construction Drawing Errors
Projects face expensive change orders because of incomplete construction plans. Design deviations make up 79% of total deviation costs and 9.5% of total project costs. Architects who lack experience with complex projects or rush through designs cause most of these errors.
Different disciplines often face coordination challenges. Structural drawings sometimes clash with mechanical layouts. This creates impossible situations where ducts run through steel beams. Problems pop up when architectural drawings don't match mechanical or electrical plans.
Design firms spend 25-50% of their time redoing completed work. Teams catch mistakes during design reviews or find conflicts between building systems that need fixes.
Shop Drawing Pitfalls
Poor model detailing and system integration lead to shop drawing errors. Small mistakes can snowball into major construction problems. Common shop drawing issues include:
- Design specifications that don't match
- Limited fabrication planning
- Trade coordination gaps
- Units and scales that don't match
Contractors who skip vital review steps face quality control problems. Unclear documentation and wrong labeling of key components also create issues.
How to Avoid Mistakes
Teams need a full document review process to build strong quality control. Key focus areas include:
- Maintaining a single repository for current plans
- Establishing clear version control procedures
- Implementing systematic drawing checks
- Creating detailed documentation standards
Premier's digital platform makes these prevention strategies easier through automated tracking and live updates. Teams can catch errors early with the software's drawing management features.
Different trades should meet regularly to prevent system conflicts. Early design phase meetings help spot potential clashes between structural, mechanical, and electrical parts.
Building Information Modeling (BIM) services help prevent more errors. Of course, these tools detect clashes and coordination issues before building starts. Digital platforms boost drawing accuracy through automated checks and efficient workflows.
Version control plays a vital role in stopping expensive mistakes. Poor version control leads to about $15 billion in yearly rework costs. Digital drawing management systems help teams track changes and keep accurate records throughout the project.
Regular drawing set audits should be part of quality assurance. Reviews help spot potential issues before they hit construction schedules or budgets. Teams must check that all drawings meet project needs and industry standards.
Comparison Table
Aspect | Construction Drawings | Shop Drawings |
---|---|---|
Created By | Architects and Engineers | Contractors, Subcontractors, Manufacturers, Suppliers |
Creation Timing | Pre-construction phase | During construction phase |
Main Goal | Project vision and structural requirements | Component details for fabrication and installation |
Detail Level | General specifications and estimated dimensions | Exact measurements and precise component details |
Core Components | - Floor plans and elevations - Structural layouts - MEP system layouts - Site plans - Material specifications | - Component dimensions - Assembly instructions - Installation guidelines - Welding specifications - Material lists |
Legal Responsibility | Design concept review and specs alignment | Measurement accuracy and contract compliance |
Review Process | Design concept conformity checks | Quality checks at multiple stages before fabrication |
Common Problems | - System conflicts - Incomplete plans - Coordination gaps | - Spec misalignment - Trade coordination gaps - Unit inconsistencies |
Digital Management | Premier Construction Software handles version control and distribution | Premier's platform tracks approvals and revisions |
Approval Requirements | Building permits and code compliance | Architect/Engineer approval before fabrication |
Conclusion
Shop drawings and construction drawings play different but complementary roles in the building process. Construction drawings show the project's vision and requirements. Shop drawings turn these concepts into detailed manufacturing instructions.
Construction management software solutions like Premier make drawing workflows efficient through automated version control and up-to-the-minute data analysis. These tools help prevent mistakes that can get pricey when trades don't coordinate well or use outdated information.
Legal obligations affect how teams handle both types of drawings. Architects oversee the design concept, and contractors take responsibility for shop drawing accuracy and field measurements. Systematic reviews and approvals protect everyone through quality control processes.
Construction projects' success depends on clear communication between these drawing types. Teams need to understand their differences and keep proper documentation throughout the project's lifecycle. Premier's drawing management platform helps construction teams track changes, control versions, and coordinate with all stakeholders.
Good understanding and handling of both drawing types guides projects toward smoother execution with fewer errors and better results. Construction professionals who grasp these differences set themselves up for greater project success.
Latest articles
Trusted by global leaders
Join those who have put their trust in us