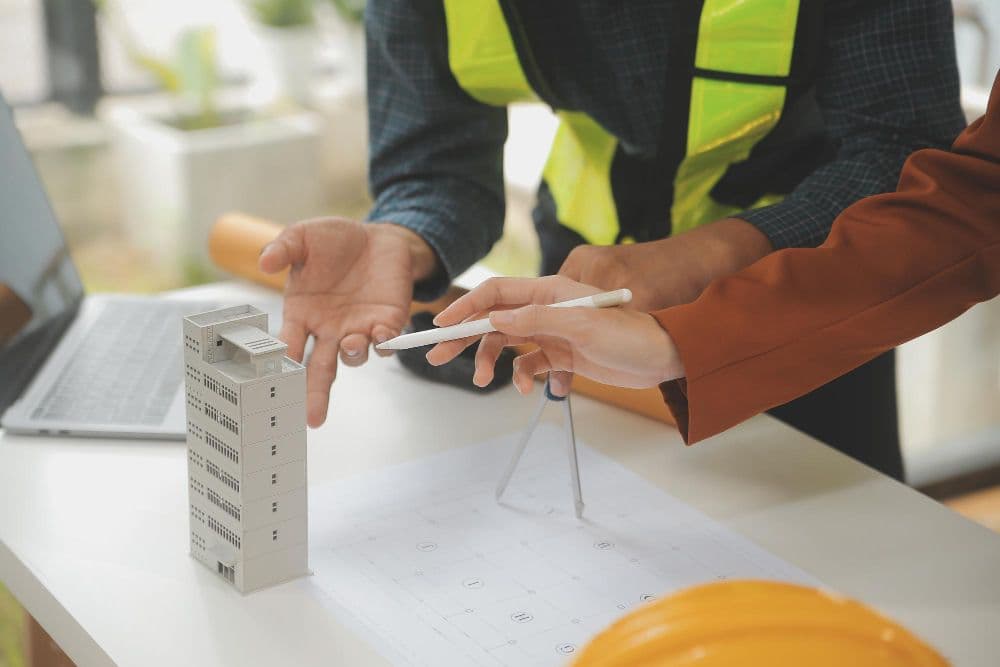
Construction Pain Points: Essential Guide for Project Managers
Construction challenges lurk around every corner of our industry, with over 91% of projects either exceeding budget or falling behind schedule—sometimes both. As project managers, we constantly navigate these hurdles while trying to deliver successful outcomes for our clients and teams.
Despite construction spending increasing in recent years, ineffective communication remains a leading cause of delays and cost overruns, affecting approximately 40% of construction projects. Additionally, we face significant regulatory pressures, with non-compliance increasing project costs by an average of 15%. The stakes are particularly high when it comes to safety, as construction-related fatalities account for about 20% of all work-related deaths.
In this guide, we'll explore the most common problems in construction industry operations and provide practical solutions for project managers. From miscommunication issues to stakeholder complexities, regulatory challenges to budget creep—we'll tackle the pain points that keep construction professionals awake at night and share strategies to overcome them.
Miscommunication and Lack of Visibility
"Today, excellent companies realize that project failures have more to do with behavioural shortcomings — poor employee morale, negative human relations, low productivity, and lack of commitment." — Harold Kerzner, PhD, Senior Executive Director for Project Management at International Institute for Learning.
Poor communication hurts construction projects in measurable ways. Recent studies reveal that one in five construction projects fails due to communication breakdowns, and nearly 48% of all rework happens because of miscommunication. This directly impacts your bottom line and creates unnecessary headaches for everyone involved.
Why field and office teams fall out of sync
Field and office teams often operate in separate worlds. Office staff rarely visit jobsites, while field workers don't see the backend complexities of coordinating with suppliers, designers, and owners. This disconnect creates friction points when information doesn't flow smoothly between locations.
Common issues include:
- Loss of critical data when field incidents go unreported
- Schedule conflicts pushing back completion timelines
- Costly errors from working with outdated information
The divide deepens when teams use different communication methods—field crews relying on texts and verbal updates while office staff work with various systems to track orders, invoices, and progress. Without a unified platform, this hodgepodge approach creates data silos and delays.
How unclear scopes and updates derail progress
Unclear project scopes create perfect conditions for trouble. When general contractors fail to communicate work requirements thoroughly with specialty contractors, scope gaps emerge. These gaps trigger a cascade of problems:
- Schedule deviations and delays
- Cost overruns
- Reduced work quality
- Extra administrative work
- Damaged relationships
Furthermore, scope creep significantly decreases project success rates. Organizational factors of scope creep have the highest negative impact, followed by human and technical aspects. Project complexity makes this worse, as more complex projects face even lower chances of success when scope issues arise.
Tools that help keep everyone on the same page
Modern technology offers solutions to these communication challenges. The most effective approach is creating a "single source of truth"—a centralized repository where all project data remains up-to-date and accessible to everyone.
Project management software integrates communication functions into one platform with features like:
- Task management and document sharing
- Real-time updates and notifications
- Progress tracking
- Mobile accessibility for field teams
Regular meetings also play a crucial role, including daily check-ins for quick updates and scheduled progress meetings to address issues promptly. Video conferencing tools enable remote engineers to view site conditions through mobile cameras, while field supervisors can review shared plans in real time.
By implementing these communication strategies, your team can avoid the 52% of rework caused by teams working with outdated information.
Stakeholder Complexity and Conflicting Priorities
Every construction project brings together a complex web of stakeholders with competing goals. Large commercial projects typically involve 5-20 distinct stakeholder groups throughout the project lifecycle. These relationships can make or break your project.
Identifying all key players early
Successful projects begin with thorough stakeholder mapping. Stakeholders generally fall into two categories:
- Internal (direct): Owners, contractors, architects, project managers
- External (indirect): Regulatory bodies, community members, local businesses
Initially, create a comprehensive stakeholder registry that includes contact information, roles, and responsibilities. This prevents overlooking critical parties who might derail your project later. Beyond the prominent players, pay special attention to those "involuntarily affected" by your work—like neighbouring businesses or residents.
Managing competing interests and expectations
Construction projects inherently create tension between time, cost, and scope—the "Iron Triangle." Effective communication helps balance these competing constraints.
Construction disputes often arise from stakeholders' misaligned expectations. For instance, when contractors have affiliations with sponsors or lenders, conflicts of interest can compromise decision-making. Moreover, owners, architects, and contractors frequently have different financial incentives that clash without proper management.
Establish a hierarchy of decision-making authority early. Document who has sign-off power at each project stage to prevent power struggles later. This clarity becomes especially important when change orders arise or when project priorities shift.
Using communication plans to reduce friction
A formal communication plan transforms how stakeholders interact. Your plan should address:
- What information each stakeholder needs
- When they need it
- Who delivers it
- How it's delivered
Accordingly, implement a conflict management strategy before disputes arise. Regular status updates keep everyone informed about project health, accomplishments, and challenges. For complex stakeholder relationships, consider using specialized construction CRM tools that centralize contact information and communication history.
Remember that proper engagement with affected stakeholders helps them understand the "why" behind challenging situations, making acceptance easier even when the news isn't positive.
Regulatory and Compliance Pressures
The regulatory landscape in construction presents a minefield of compliance requirements. Construction teams face numerous safety hazards—from falls and electrical risks to silica dust exposure. Consequently, regulatory bodies continuously update their standards to protect workers.
Keeping up with changing safety and environmental rules
OSHA frequently updates its regulations, requiring construction firms to adapt quickly. Environmental regulations further complicate matters, with requirements around stormwater management, waste disposal, and air quality. These evolving standards create substantial overhead, as non-compliance can lead to project shutdowns.
Avoiding fines and delays through documentation
The financial stakes are substantial—willful violations can result in penalties up to $161,323 per violation, while serious violations carry fines exceeding $16,131 each. Environmental infractions may cost up to $27,500 per day.
To minimize these risks:
- Maintain accurate injury and illness records
- Document safety inspections regularly
- Follow-up conversations with written summaries
- Keep photographic evidence of site conditions
Training teams to stay compliant
Proper training remains the cornerstone of compliance. OSHA mandates that workers receive education on hazard recognition, equipment usage, and emergency procedures. For construction firms, OSHA 10-hour and 30-hour programs provide essential safety education.
Throughout this process, technology solutions can streamline compliance management through centralized document storage and mobile accessibility.
Change Orders, Budget Creep, and Scheduling Chaos
"Project management can be defined as a way of developing structure in a complex project, where the independent variables of time, cost, resources, and human behaviour come together." — Rory Burke, Project management author and consultant.
Change orders represent one of the most persistent challenges in construction, occurring in virtually every project. Large projects typically experience between 5 and 11 change orders throughout their lifecycle. These modifications commonly inflate budgets 5-10%, [costing the industry approximately $44 billion annually] (https://peer.asee.org/change-orders-impact-on-project-cost.pdf).
Why change orders happen more than you think
Even with careful planning, change orders remain inevitable. Common triggers include:
- Unforeseen site conditions like unexpected utilities or structural issues
- Incomplete or inaccurate initial plans
- Client-requested modifications after construction begins
- Regulatory compliance discoveries
- Material shortages or supply chain disruptions
Over 75% of change orders stem from scope creep or poorly defined project parameters, highlighting the importance of clear initial documentation.
How they impact labour, materials, and timelines
The ripple effects of change orders extend throughout projects. According to McKinsey, construction projects typically finish 20% behind schedule and up to 80% over budget. These modifications disrupt workflows, requiring rescheduling of subcontractors and reallocation of resources. Subsequently, each change can trigger cascading delays as interconnected tasks shift.
Planning to reduce surprises
To minimize change order impacts, establish a structured approval process including:
- Standardized documentation templates outlining cost implications and schedule effects
- Multi-tiered approvals involving all key stakeholders
- Regular budget reviews with visual alerts for potential overruns
Thorough site investigations during preconstruction
Key Takeaways
Construction project managers face predictable challenges that can be systematically addressed with the right strategies and tools.
• Communication breakdowns cause 48% of construction rework - Implement centralized project management systems to keep field and office teams synchronized with real-time updates.
• Stakeholder mapping prevents costly disputes - Identify all internal and external stakeholders early, establish clear decision-making hierarchies, and create formal communication plans.
• Regulatory non-compliance increases project costs by 15% - Maintain thorough documentation, provide mandatory safety training, and stay current with evolving OSHA and environmental regulations.
• Change orders inflate budgets 5-10% on average - Establish structured approval processes, conduct thorough site investigations during preconstruction, and use standardized documentation templates.
• 91% of construction projects exceed budget or fall behind schedule - Success requires anticipating challenges through proper planning, centralized systems, and proactive stakeholder management.
The construction industry's challenges are well-documented, but they're also solvable. By addressing communication gaps, managing stakeholder complexity, maintaining compliance, and controlling change orders, project managers can significantly improve their success rates and deliver projects on time and within budget.
FAQs
Q1. What are the main causes of construction project delays and budget overruns? The primary causes include miscommunication between field and office teams, unclear project scopes, stakeholder conflicts, regulatory non-compliance, and frequent change orders. Poor communication alone can lead to 40% of projects experiencing delays and cost overruns.
Q2. How can project managers improve communication in construction projects? Project managers can implement a centralized project management system that serves as a "single source of truth," conduct regular team meetings, use video conferencing for remote site inspections, and ensure all team members have access to up-to-date project information through mobile-friendly platforms.
Q3. What strategies help in managing stakeholder expectations in construction projects? Key strategies include early stakeholder identification and mapping, creating a comprehensive stakeholder registry, establishing clear decision-making hierarchies, and developing a formal communication plan that outlines what information each stakeholder needs, when they need it, and how it will be delivered.
Q4. How can construction firms stay compliant with changing regulations? To maintain compliance, firms should regularly update their knowledge of OSHA and environmental regulations, provide mandatory safety training to workers, maintain accurate documentation of safety inspections and incident reports, and consider using technology solutions for centralized compliance management.
Q5. What is the impact of change orders on construction projects, and how can they be managed? Change orders typically inflate project budgets by 5-10% and can cause significant scheduling disruptions. To manage them effectively, establish a structured approval process with standardized documentation templates, involve all key stakeholders in approvals, conduct regular budget reviews, and perform thorough site investigations during the preconstruction phase to minimize surprises.
Latest articles
Trusted by global leaders
Join those who have put their trust in us