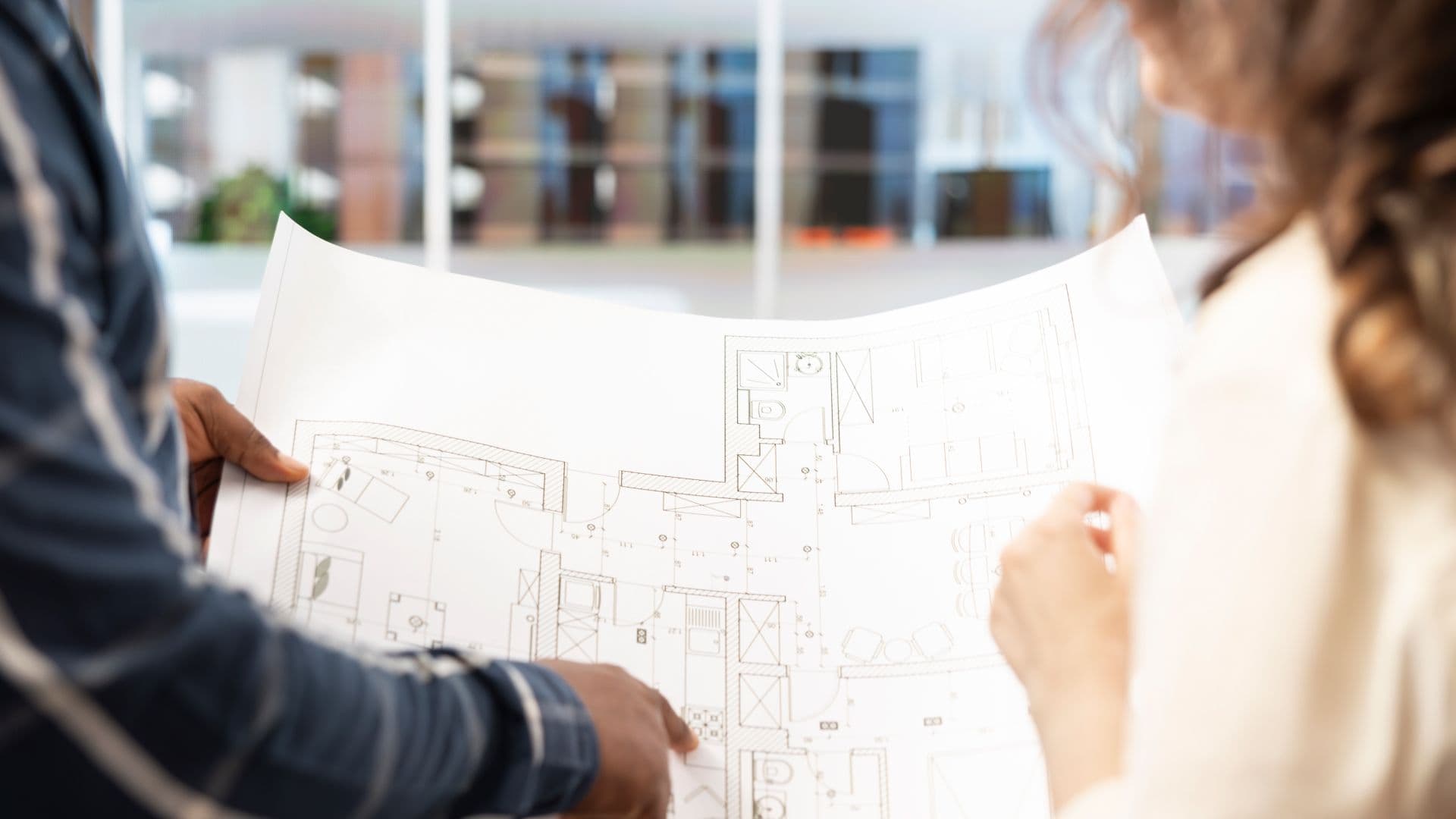
Construction Drawings Explained: An Architect's Guide to Blueprint Basics
Construction drawings work as the universal language of building projects and serve as a vital communication tool between architects, engineers, and contractors. These detailed graphical representations were known as blueprints in the past. They show everything from wall locations to window placements and help prevent errors that can get pricey and delay projects.
A complete construction drawing set has floor plans, elevations, sections, and specific detail drawings that guide the building process. Building Information Modeling (BIM) software has transformed these drawings from simple 2D representations into complete 3D models. The models improve accuracy and identify potential issues early. The specialized mechanical, electrical, and plumbing (MEP) drawings detail the infrastructure systems and create a complete picture of the final building.
This piece breaks down everything in construction drawings and explains how they guide projects from the original concept through final construction. You will find how to interpret different drawing types, understand standard symbols, and follow the progression from schematic design to final construction documents.
Basic Components of Blueprint Reading
Construction drawing interpretation relies on two key elements: the title block and drawing notes with legends. These are the foundations of understanding architectural blueprints.
Title Block Information
You'll find the title block at the lower right corner of each construction drawing sheet. This standard section holds vital project details that identify and verify the document. The title block must include the drawing number, project title, firm details, original scale, and general specifications.
A well-laid-out title block shows:
- Project identification (name, address, location)
- Drawing details (title, scale, date)
- Professional information (architect name, license number)
- Sheet numbers and references
- Revision history tracking
The title block's placement follows specific conventions. Architects place it on the right side since construction documents bind on the left. This makes it easy to flip through and find information.
Drawing Notes and Legends
Drawing notes provide clear explanations that enhance the graphical elements of construction blueprints. These notes come in two types: general notes that apply to the entire project and local notes that point to specific features.
Architects usually place general notes centrally below the relevant view or in a dedicated column. These notes cover everything from finishing requirements to universal specifications. Local notes link directly to individual features through leader lines and give exact details about dimensions, materials, or installation needs.
Legends work like a decoder for construction drawings. They explain the symbols, line types, and abbreviations used throughout the document. Each drawing type—electrical, plumbing, or structural—uses its own set of standard symbols that legends help decode.
Today's drawing management systems make organizing and accessing these components easier. Teams can track changes, handle revisions, and keep notation consistent in all project documents with software solutions.
Construction drawings work best with proper implementation of these simple components. Architects who maintain clear title blocks and complete legends create documents that communicate clearly at every construction stage.
Site Drawing Fundamentals
Site drawings are the foundations of construction projects. They show significant elements that determine building placement and development. These detailed plans help architects and contractors navigate the complex process of site development.
Property Lines and Setbacks
Property lines mark legal boundaries. Setbacks create mandatory spaces between structures and these boundaries. Front yard setbacks range from 25 to 30 feet from the property line. Side setbacks usually span 10 feet on each side. Rear setbacks help maintain privacy between neighboring properties.
Common setback types include:
- Front yard setbacks for street-facing facades
- Side yard setbacks for spacing between buildings
- Rear yard setbacks for backyard space
- Waterfront setbacks for environmental protection
Failing to meet setback requirements results in fines and possible structure changes. Local zoning ordinances set specific measurements that affect property value and buildable area.
Topography Representation
Topographical features show up through contour lines on site drawings that display elevation changes and natural formations. These lines run perpendicular to the slope direction and reveal the terrain's steepness. Architects study these patterns to find the best building placement and drainage solutions.
The datum point works as a reference for all elevation measurements. Contour lines predict water flow patterns across the site and shape drainage system design and erosion prevention. This information helps teams choose foundation types and construction methods.
Utility Locations
Underground utilities need careful planning and coordination. Water mains and sanitary sewers must maintain a 10-foot horizontal separation. Electric, gas, telephone, and cable television lines create an intricate network of services underground.
Teams must check existing utility locations before construction begins. Premier's drawing management software helps track these utility placements and keeps documentation current throughout project phases.
Drainage in grassed areas needs a minimum 2% slope, while paved areas require at least 0.75%. The site's drainage patterns determine utility connection placement and infrastructure development.
Floor Plan Development Steps
Floor plan development needs close attention to spatial relationships and functional design principles. A good floor plan strikes a balance between daily activities and optimal space use. This creates environments that support their intended purposes.
Room Layout Principles
Space allocation depends on how each area will function. Living areas need a natural flow from private to public spaces. Architects study how different spaces work together to create a design that serves the occupants' needs.
These are the significant principles to create an effective room layout:
- Defining clear traffic flow patterns between spaces
- Maximizing natural light through strategic window placement
- Creating balanced proportions between connected areas
- Incorporating flexible, multifunctional spaces
- Establishing proper dimensions for furniture placement
Room dimensions affect the overall functionality. To cite an instance, dining rooms need enough space for furniture and comfortable movement. As with living areas, proper ceiling heights and dimensions help maintain visual harmony.
Door and Window Placement
Door and window positions affect both functionality and comfort. Windows on opposing walls give the best cross-ventilation and natural light flow. Rooms with tall ceilings and large volumes work best with high-positioned windows.
Door placement follows specific guidelines for smooth flow. The standard pathway width measures 36 inches minimum. Main hallways work better with 42-48 inches. This spacing lets people move easily between rooms while keeping their privacy.
Window placement affects energy efficiency and comfort. South-facing windows capture useful winter sunlight, and proper overhangs block harsh summer rays. Well-placed windows cut down on artificial lighting needs and connect indoor spaces with the outdoors.
Premier's drawing management software helps teams track these vital placement decisions during design. The software keeps accurate records of door and window specifications and supports smooth collaboration between architects and contractors.
Accurate dimensions are vital for door and window installation. Architects typically draw locations to the center point. This gives flexibility for different sizes and trim options. The approach stays accurate no matter what fixture selections or molding specifications are chosen.
Doors and windows work together to shape the room's atmosphere. Their position depends on furniture placement, traffic patterns, and visual balance. Smart placement creates welcoming spaces that serve their purpose well.
Elevation Drawing Techniques
Elevation drawings show architectural concepts as precise vertical views of buildings. These technical documents display exterior views from different angles that capture height, width, and design elements shaping the final structure.
Exterior View Creation
Architects start creating exterior views by looking at floor plans to locate wall corners, openings, and key features. Hand-drawn elevations let architects express artistic style through linework and shading. CAD software gives precise drafting and makes modifications easier.
The process works like this:
- Vertical projections arranged with floor plan edges
- Window and door locations marked precisely
- Material textures and architectural details added
- Annotations for dimensions and specifications
Digital tools improve the process with rendering capabilities. These programs add textures, lighting effects, and shadows to create photorealistic images. Premier's construction drawing management software makes this process smooth by keeping accurate documentation throughout design phases.
Height and Width Measurements
Height and width measurements just need to follow scale and proportion standards. A typical building has a ceiling height of 10 feet, while doors measure at least 80 inches tall. You'll find these measurements on elevation drawings through dimension lines and text callouts.
Proportional relationships use these principles:
- The golden ratio (1:1.618)
- The Fibonacci sequence
- Standard architectural scales of 1:100 or 1:50
Elevation drawings show:
- Floor-to-ceiling heights
- Window and door dimensions
- Roof slopes and overhangs
- Material transitions
- Ground level indicators
Each elevation view shows its facing direction, like "rear (south)". Architects include outline elevations of nearby buildings that could affect the design. This helps everyone see how new structures blend with existing surroundings.
Material specs appear right on elevation drawings with colors and types of finishing materials. These notes cover everything from brick types to roof tiles that give contractors clear guidance for construction.
Property boundary lines stay visible on elevation drawings. This helps check setback rules and space between structures. Architects also mark building elements for demolition to communicate clearly during renovation projects.
Section Drawing Creation Guide
Section drawings show what's inside buildings through vertical cuts. These specialized drawings work as virtual examinations that display hidden structural elements and how spaces connect to each other.
Cutting Plane Selection
The cutting plane shows which building elements you'll see in the section view. This imaginary plane cuts through the structure and usually follows a straight line. Architects choose cutting planes based on these reasons:
- Full sections - complete vertical slice through the building
- Half sections - showing both interior and exterior views
- Offset sections - incorporating multiple angles
- Broken sections - focusing on specific areas
- Revolved sections - displaying cross-sectional features
The cutting plane line appears as a thick dashed line (0.6 mm) on drawings and extends 6mm past the object edges. Arrows at the ends show the viewing direction and point away from the sectioned view. Architects place the cutting plane to capture key building features like stairs, structural elements, or unique spatial layouts.
Detail Level Requirements
Section drawings need specific details based on their purpose. Wall sections highlight material layers and connections. Site sections show how buildings relate to the surrounding terrain. Premier's drawing management software helps teams keep consistent detail levels in all section types.
Technical requirements for section drawings include:
Standard line weights separate elements - bold lines show major architectural components while fine lines indicate minor details. Poche techniques fill cut components with patterns or shading to show different materials. This adds depth perception and helps understand spaces better.
Section drawings leave out hidden lines unless they're crucial. Thin walls, ribs, and similar features stay unsectioned when cut parallel to their length. This stops materials from looking thicker than they are.
Detail sections zero in on specific building parts and show construction methods and material connections. These drawings use larger scales to show complex assemblies and joints. They have notes that describe materials, dimensions, and installation steps.
The detail level changes by section type:
- Building sections - show overall spatial organization
- Wall sections - display material layers and connections
- Site sections - illustrate topography and building relationships
Section drawings use furniture and fixtures to help show scale. These elements help people understand room sizes and how spaces work. Light and shadow details show how natural light moves through spaces.
Material Specifications in Drawings
Material specifications are the foundations of construction documentation that provide exact details about building components and finishes. These specifications turn design intent into practical construction information.
Wall Section Details
Wall sections show how building walls are put together vertically through detailed cross-sectional views. Each layer shows up in exact scale, from interior finishes all the way to exterior cladding. Architects typically use a scale between 1:10 and 1:20, which makes individual components clearly visible.
Architects start by drawing the simple wall outline at their chosen scale. They then add structural elements like studs or concrete blocks. More layers come next - internal finishes, insulation, sheathing, and external cladding. Premier's drawing management software helps teams keep track of these complex wall assemblies throughout the project.
Wall sections must have these critical elements:
- Structural components and spacing
- Insulation and vapor barriers
- Connection details between materials
- Waterproofing specifications
- Exterior finish attachments
Finish Schedule Creation
Finish schedules put material specifications into well-laid-out tables that detail finishes for floors, walls, and ceilings. These schedules give specific information about product names, model numbers, sizes, and finishes.
A detailed finish schedule has room numbers for every space. Architects split walls into north, south, east, and west orientations to allocate materials precisely. This method helps estimate costs accurately and procure materials efficiently.
Quality comes before price in the selection process, followed by appearance and local availability. Architects look at physical samples, technical data sheets, and high-quality product photos to make their final choices. Manufacturers' representatives and showroom visits play a key role in the specification process.
Digital platforms make finish schedule management easier. Online resources give technical specifications and application examples. All the same, using both digital tools and physical samples gets the best results for material selection.
The finish schedule matrix puts spaces on one axis and materials on another. This layout lets you quickly find what you need by floor or space type. The schedule contains manufacturer details, model numbers, and specific color selections. This organized approach helps architects communicate material requirements clearly at every project stage.
Drawing Coordination Between Teams
Construction projects succeed when teams coordinate precisely during drawing development. Shop drawing reviews connect design and construction phases through structured communication between stakeholders.
Architect-Engineer Communication
Design teams need clear role definitions to work well together. Design architects specify which items need shop drawings and check them against design intent. Project managers keep track of submissions and work out review timeframes.
Key stakeholders in the communication chain include:
- Design architects and engineers - review for design compliance
- Project managers - coordinate timelines and track progress
- Consultants - provide specialized technical input
- Structural engineers - verify structural integrity
- MEP engineers - confirm system specifications
Digital tools make architect-engineer collaboration smoother. Cloud-based documentation software creates a central hub for immediate information sharing. Team members can upload, review, and comment on drawings from anywhere.
Premier's drawing management software helps this coordination by tracking versions and changes throughout reviews. Team members receive alerts about pending reviews and upcoming deadlines.
Contractor Review Process
Contractors create a submittal schedule after receiving product specifications from architects. This schedule sets review timelines and assigns responsibilities. Reviews usually take two weeks, but some projects need faster completion.
The contractor's review responsibilities include:
- Checking constructability of proposed methods
- Assessing material feasibility
- Checking alignment with construction schedules
- Coordinating between subcontractors
- Distributing reviewed drawings
Contractors check shop drawings for constructability and focus on practical implementation rather than design changes. They verify design intent and pay close attention to site conditions and installation requirements.
Reviews need thorough documentation. Architects or engineers of record must stamp each drawing. This step shows the review's completion and confirms design compliance.
Quick turnarounds shouldn't compromise proper review time. Some elements like electrical equipment and generators need longer reviews. Rushed reviews often lead to missed issues that get pricey during construction.
Digital platforms help contractor-architect communication through automated notifications. Team members receive alerts when submittal materials are ready for the next review step. This keeps the process flowing smoothly between phases.
Team coordination goes beyond simple communication. Teams review ceiling drawings from architectural, electrical, mechanical, and fire suppression sets together to spot conflicts. This comprehensive approach catches issues before they show up on site.
Design teams must respond quickly to information requests despite tight schedules. Quick responses prevent bottlenecks and keep projects moving forward.
Construction Drawing Updates and Revisions
Construction projects evolve through drawing revisions that track changes from the original design to completion. Teams need systematic management of these changes to stay accurate and avoid getting pricey mistakes.
Change Order Documentation
Formal documentation through change orders modifies original construction contracts. These changes affect three key elements: work scope, cost adjustments, and timeline revisions. Owners, contractors, and architects must all agree to approve a change order.
Change orders fall into two distinct categories:
- Additive orders - expand project scope and increase costs
- Deductive orders - reduce scope and decrease contract value
Architects initiate the change order process through proposal requests or supplemental instructions. Contractors then submit detailed cost estimates and explain timeline effects. Premier's drawing management software makes this process smoother by keeping clear documentation trails for each modification.
Architects check contractor proposals to verify accuracy and cost justification. They focus on preventing double-counted costs or unauthorized reimbursements. The formal change order document then lists detailed descriptions, cost breakdowns, and schedule impacts.
Cloud-based systems have reshaped change order management. These systems track modifications, send automatic notifications, and keep version control. Digital tools speed up approvals and reduce errors. Contractors still need to follow contractual procedures for changes, even under field conditions.
As-Built Drawing Requirements
As-built drawings show a building's final, constructed state and document all construction modifications. These records help with future maintenance, renovations, and facility management.
As-built documentation needs specific elements:
- Accurate utility locations and routing
- Final material specifications
- Approved design modifications
- Dimensional changes
- Installation details
Contractors must keep current records throughout construction. Teams track changes live because waiting until project completion risks missing key details. Digital platforms support ongoing documentation through mobile technology and cloud storage.
As-built drawings play a vital role in legal compliance and dispute resolution. They show compliance with building codes and contract specifications. First responders also use these documents for emergency response planning.
Multiple stakeholders work together to create as-built drawings. Contractors record field changes while architects verify accuracy and compliance. Project managers help teams keep documentation current. Good as-built records help reduce future maintenance costs and support efficient building operations.
Digital tools improve as-built accuracy through:
- GPS-tagged construction photos
- Live field updates
- Automated change tracking
- Cloud-based document storage
Design teams and owner's representatives check final as-builts against change orders, RFIs, and other submittals. This verification ensures all modifications appear in the final documentation. Building owners need accurate as-built drawings to manage operations, make tenant improvements, and handle potential property sales.
Some municipalities ask for regular drawing updates during construction. Local authorities and utility companies can then quickly reference these documents. All documentation must show properly approved changes through change orders.
Conclusion
Construction drawings are the foundations of successful building projects. These detailed documents guide projects from original concept to final completion and connect architects, engineers, and contractors through standardized visual communication.
A professional drawing set combines multiple elements. Floor plans display spatial relationships, and elevation drawings show external appearances. Section drawings reveal internal compositions that provide significant insights into the building's structure. Site plans and material specifications round out this detailed package.
Project teams need careful drawing management throughout their lifecycle. Premier's construction management software helps teams track changes, coordinate reviews and maintain accurate documentation. Digital solutions reduce errors and speed up project delivery.
Technology continues to advance the construction industry. Building Information Modeling (BIM) has revolutionized traditional 2D drawings into detailed 3D models. These tools detect potential problems early and improve coordination among project stakeholders.
Project success depends on proper drawing creation and management. Clear documentation prevents projects from getting pricey, supports team collaboration and delivers better results. Teams skilled at these fundamental practices consistently achieve project success.
Latest articles
Trusted by global leaders
Join those who have put their trust in us