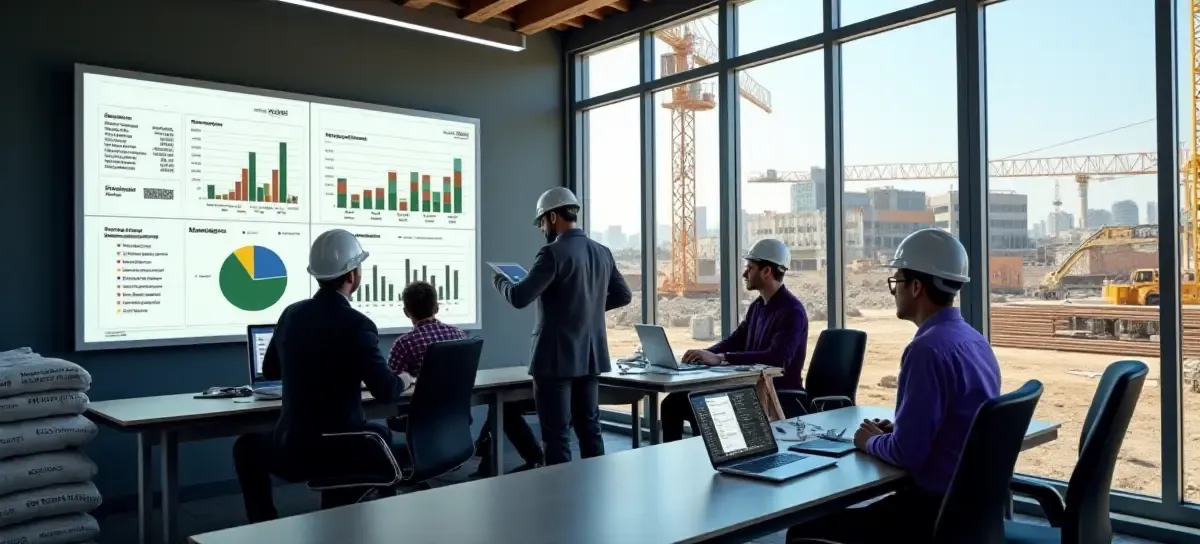
Exploring Construction ERP Modules: Key Features and Benefits
Construction companies waste 35% of their resources because of poor project management and systems that don't work together.
ERP modules give construction companies a detailed solution to simplify processes in project management, workforce coordination, and equipment control. These integrated systems help companies automate their work, cut down errors, and boost efficiency. Premier construction management software’s ERP modules show how digital tools can revolutionize construction operations with live data access and automated processes.
Modern cloud-based construction ERP modules let teams run projects from anywhere while they retain control of data security and consistency. Construction ERP modules come with features for project scheduling, document management, resource allocation, and financial control. Let's get into the must-have ERP modules for construction companies, their standout features, and how they improve construction operations of all sizes.
Project Management Excellence
Project management modules are the life-blood of construction ERP systems. Over 90% of large businesses use these solutions to improve their operations.
Timeline Management
Construction ERP modules have changed project timelines into powerful management tools. Project managers can see tasks in calendar formats, find dependencies, and spot potential bottlenecks. Teams can now:
● Track daily, weekly, and monthly activities
● Monitor project costs and resource allocation
● Get up-to-the-minute progress reports
● Switch between quarterly and weekly schedule views
Document Control Systems
A centralized document control system forms the foundations for successful project execution. Cloud-based repositories give construction teams quick access to current project documentation. The system indexes records automatically and keeps version control for all project files.
Document management features handle different file types and offer unlimited storage. This digital approach removes paper documentation risks and creates efficient project control. Teams view, mark up, and share construction drawings while keeping clear audit trails.
Change Order Processing
Change orders substantially affect project timelines and budgets. The GAO confirms that delayed change orders disrupt cash flow and create challenges, especially when you have small construction firms.
Construction ERP modules make the change order process efficient through automated workflows. The system records every project transaction, which helps track:
● Contract modifications
● Cost adjustments
● Timeline revisions
● Scope changes
Premier Construction Software's ERP modules show how digital solutions speed up change order processing. The system keeps detailed records of modifications, supporting documentation, and approval workflows. Construction teams process changes quickly and maintain accurate project records with this systematic approach.
Project managers track change orders from start to approval, and project budgets and schedules update automatically. This integration prevents delays and keeps communication clear between stakeholders.
Workforce Management Solutions
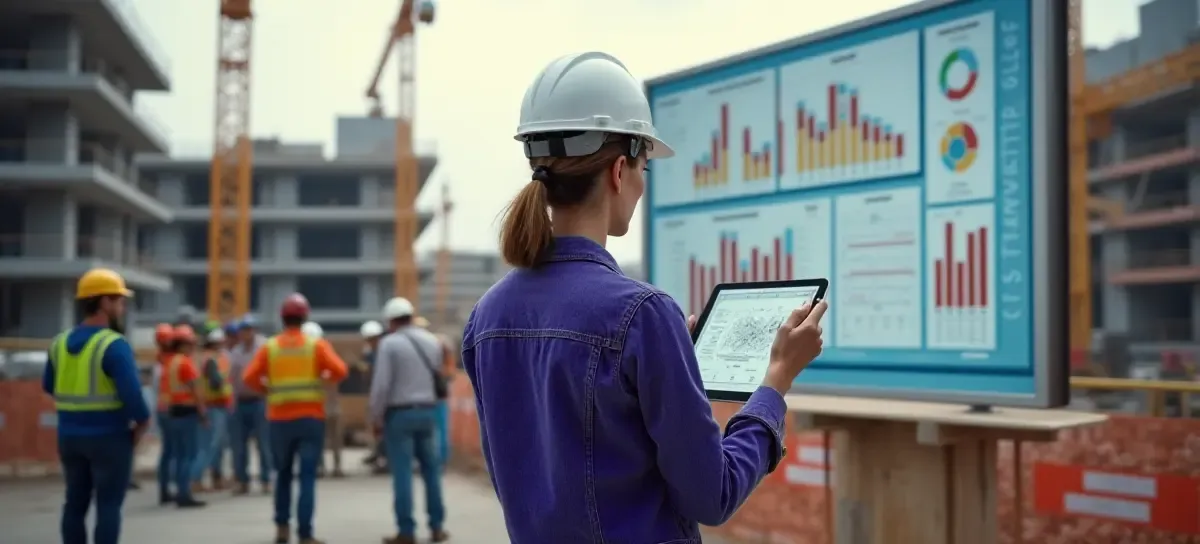
Digital innovation and automation help construction ERP modules change workforce management. Research shows that construction companies using digital workforce solutions can reduce administrative time by up to 80%.
Employee Scheduling
Digital platforms have changed how construction crews manage and allocate resources. Managers can create, modify, and share schedules with a click. Teams get instant notifications about changes and assignments. The system provides:
● Up-to-the-minute schedule updates and changes
● Automated conflict detection
● Multi-site crew coordination
● Mobile accessibility for field teams
Skills Matrix Management
Skills matrices enable construction companies to map employee capabilities and build better teams. Studies show that companies using skills matrices make smarter decisions about talent deployment. The system keeps track of individual competencies, certifications, and growth opportunities.
Better project outcomes result from construction companies that use skills matrices to line up their teams. The system helps managers spot skill gaps and create focused training programs. Worker certifications and completed training modules update the digital matrix automatically.
Premier Construction Software combines skills tracking with project requirements to match qualified personnel with specific tasks. This combination cuts down project delays and maintains quality control through proper resource allocation.
Time and Attendance Tracking
New time tracking solutions do away with paper timesheets and minimize wage calculation errors. The US Bureau of Labor Statistics shows that construction companies deal with average daily absence rates between 3.2% and 3.6%. Digital tracking systems let managers monitor these patterns and take quick action.
Construction ERP modules use GPS-enabled time tracking and biometric verification. These tools prevent time theft and ensure accurate payroll. Workers can clock in from job sites using mobile apps, while geofencing technology checks their location.
SHRM research estimates unplanned absences cause a 36.6% drop in productivity, while planned absences lead to a 22.6% reduction. Digital attendance systems help construction managers reduce these effects through smart workforce planning and quick adjustments.
Time tracking and project management modules work together to show a complete picture of labor use. Managers can study productivity trends, adjust crew sizes, and predict labor needs accurately. This analytical approach helps construction companies maintain the right staffing levels across multiple projects.
Client Relationship Tools
Strong client relationships lead to construction success. Modern construction ERP modules revolutionize client interactions through digital tools and automated processes.
Communication Portals
Digital client portals optimize project communications and boost transparency. These platforms generate a 41% response rate for client interactions, which is by a lot higher than traditional methods. Construction teams can share:
● Live project updates
● Progress photos and reports
● Budget tracking information
● Schedule modifications
● Document approvals
Contract Management
Advanced contract management tools cut processing time and minimize errors. Construction ERP modules automate contract workflows and maintain detailed audit trails. The system tracks contract changes and helps companies prevent the 9% revenue loss that comes from poor contract terms.
Premier Construction Software's contract management speeds up approvals through electronic signatures. This digital approach reduces contract processing from weeks to minutes. The system updates related project schedules and budgets automatically when contract changes happen.
Client Feedback Systems
Client feedback tools help construction companies measure satisfaction and fix issues quickly. These systems cut repeat client frustrations by 83%. Construction teams get instant alerts when feedback needs attention, which lets them respond fast to client needs.
Digital feedback platforms double the standard response rates and reveal six times more practical insights. This higher participation helps construction companies spot trends and deliver better service. Companies that use systematic feedback tools earn $1.8 million in new business through referrals.
The blend of communication, contract management, and feedback systems creates a detailed view of client relationships. Project managers can track client priorities, monitor satisfaction levels, and keep clear records of all interactions. This connected approach helps construction teams deliver great service and build lasting client partnerships.
Equipment and Asset Control
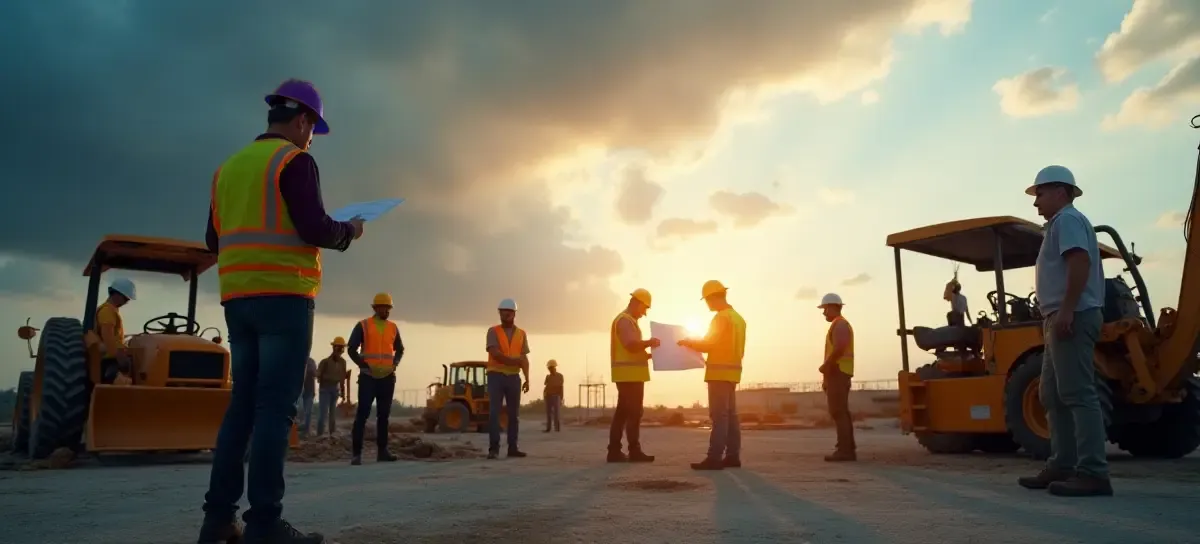
Equipment management plays a vital role in construction project success. Construction ERP modules are changing how companies track and maintain their valuable assets.
Maintenance Scheduling
Digital maintenance systems cut equipment downtime by up to 30% with automated scheduling. Construction ERP modules optimize maintenance operations through:
● Automated service alerts based on usage hours
● Digital work order generation
● Preventive maintenance scheduling
● Up-to-the-minute maintenance history tracking
● Compliance documentation management
Premier Construction Software's maintenance scheduling features help construction teams avoid breakdowns that get pricey. The system tracks service intervals and notifies teams when maintenance is due.
Equipment Utilization Tracking
GPS-enabled tracking systems show where equipment is and how it's being used. Companies that use utilization tracking save an average of $30,000 in equipment rental fees. Construction teams learn about:
Equipment utilization rates help teams spot underused assets and optimize resource allocation. Studies show proper utilization tracking can cut idle time costs by $400,000 each year.
Modern telematics systems watch fault codes and performance metrics as they happen. This data helps maintenance teams spot issues remotely and fix them faster. The system logs operating hours, which leads to better maintenance scheduling and cost tracking.
Asset Lifecycle Management
Detailed lifecycle management begins with equipment acquisition and runs through disposal. Construction ERP modules keep records of:
1. Purchase and warranty information
2. Maintenance history and costs
3. Utilization rates and performance data
4. Depreciation calculations
5. Operating expenses
Digital asset management cuts unscheduled downtime to less than 10% of total working time. Construction teams can make evidence-based decisions about equipment replacement and resource allocation.
Construction companies that use integrated asset management see better equipment reliability. Regular maintenance tracking helps equipment last longer and reduces emergency repair costs. The system updates financial modules with equipment expenses, giving accurate project cost data.
GPS tracking and geofencing technology add better security. Managers get instant alerts when equipment moves outside designated areas. This feature stops theft and unauthorized use while keeping location records accurate.
Cloud-based construction ERP modules let field teams and office staff work together. Workers can update equipment status, report issues, and check maintenance records from anywhere. This smooth connection speeds up response times for equipment problems.
Compliance and Safety Features
Modern construction operations depend on safety and compliance as their foundation. Construction ERP modules have revolutionized the way companies handle safety protocols and regulatory compliance.
Safety Protocol Management
Construction ERP systems make safety management better through automated monitoring and live alerts. These digital solutions reduce accident rates by a lot. Companies using integrated safety systems have seen workplace incidents drop by up to 85%. Premier Construction Software's safety modules include:
● Automated safety inspection scheduling
● Digital safety training records
● Live hazard notifications
● PPE compliance tracking
● Emergency response protocols
The system schedules safety training sessions and keeps attendance records automatically. This digital approach creates clear documentation of all safety activities and builds a proactive safety culture.
Regulatory Compliance Tools
Construction ERP modules make regulatory compliance easier with automated monitoring and documentation. Digital compliance tools help companies reduce penalties linked to non-compliance.
The system keeps safety standards current by:
1. Automating regulatory updates
2. Tracking certification renewals
3. Managing compliance documentation
4. Monitoring safety inspection schedules
5. Generating compliance reports
Teams get immediate access to updated OSHA guidelines and safety protocols. The software flags potential compliance issues and notifies when certifications need renewal.
Incident Reporting Systems
Digital incident reporting has changed how construction companies document and analyze safety events. ERP modules allow teams to document incidents as they happen, which helps with quick response and detailed investigation.
The system records detailed incident information, such as:
● Location and time stamps
● Involved personnel
● Witness statements
● Photo documentation
● Corrective actions taken
Construction companies that use digital incident reporting respond faster and conduct better investigations. The software alerts the core team when incidents occur, which speeds up emergency resource deployment.
Data analysis tools spot patterns in incident reports to prevent future problems. Companies using these analytical features have cut repeat incidents by 30%. The system creates complete reports to review management and submit to regulators.
Premier's incident management module makes the entire reporting process smoother. Teams can document incidents on their mobile devices, add supporting evidence, and watch investigation progress live.
Construction ERP modules blend safety protocols with daily operations. Companies can stay compliant while making operations more efficient. The software updates safety documentation, tracks training needs, and watches for regulatory changes.
Digital compliance tools cut down on paperwork and improve accuracy. Construction teams save 15-20 hours each week on compliance tasks. The system keeps detailed audit trails that make regulatory inspections and internal reviews simpler.
Field teams get safety alerts instantly through mobile apps. Quick communication prevents accidents and helps teams respond fast to possible hazards. The software tracks who sees these alerts and keeps clear records of safety communications.
Conclusion
ERP modules have changed traditional construction management into an optimized, informed operation. These integrated systems bring measurable improvements to critical business areas.
Project managers handle complex schedules, documents, and change orders through automated workflows. Digital workforce solutions cut administrative time by 80%, and you retain precise control over scheduling and attendance. Digital portals have improved client communication with 41% higher response rates.
Smart maintenance scheduling and GPS tracking help equipment management systems reduce downtime by 30%. Safety results are equally impressive. Companies see up to 85% fewer workplace incidents after they implement digital safety systems.
Premier Construction Software shows these benefits through its complete ERP solution. Their platform connects every part of construction operations from project planning to equipment tracking. Construction teams that use integrated ERP systems report improved productivity, better cost control, and faster project delivery times.
Today's construction needs modern solutions. ERP modules are the digital foundation needed to succeed in construction. Companies that accept these technologies grow steadily while keeping high standards of safety and client satisfaction.
Latest articles
Trusted by global leaders
Join those who have put their trust in us