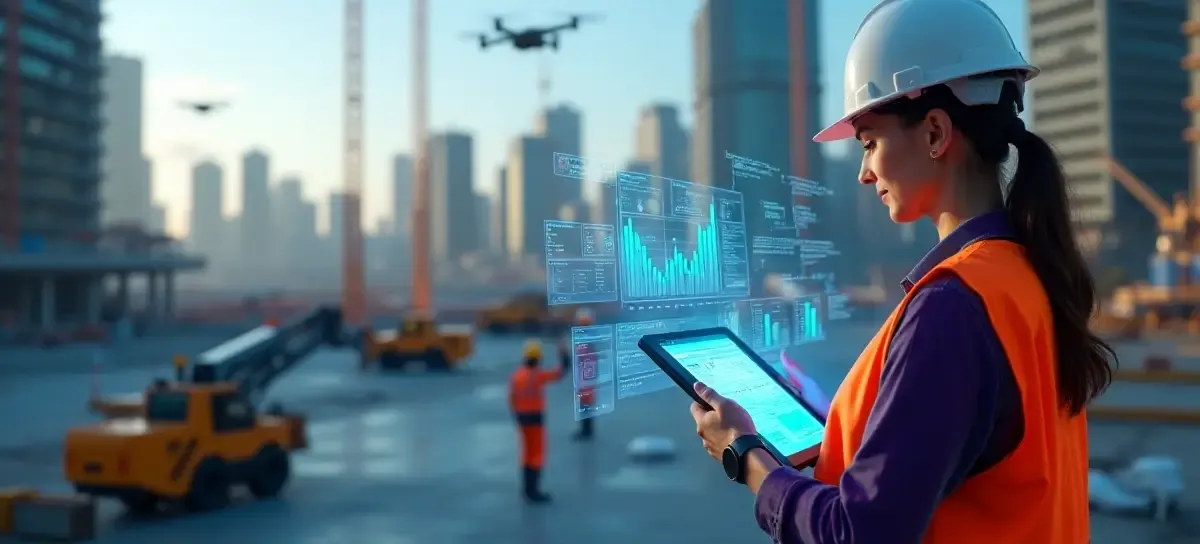
7 Essential Construction Project Management Tips
Recent industry data shows that construction projects fail 85% of the time because of poor management practices. This statistic expresses why project management tips are significant to succeed in 2024.
Construction industry professionals deal with unique challenges in meeting deadlines, managing budgets and coordinating teams. Premier Construction Software offers modern solutions that help managers optimize their operations through digital tools and automated processes. These improvements have made construction project management easier than before.
This piece covers seven vital tips that blend traditional project management knowledge with innovative technology. These strategies help construction managers complete projects on schedule and within budget through better resource allocation and risk management.
Digital Tools Transform Project Planning
Digital tools play a vital role in today's construction project management. Recent data shows 90% of construction professionals think mobile applications are essential to their current processes.
Selecting the right project management software
Project managers need to review software based on these key factors:
● Immediate data access
● Cloud-based collaboration features
● Integration capabilities
● Mobile device compatibility
● Budget-friendly options
● Accessible interface
Integration with Premier Construction Software
Premier’s construction project management software distinguishes itself with its AI-powered platform that links every part of construction operations. The system combines financial management, project planning, and job costing through one interface.
Teams get immediate project updates and work together naturally through API integrations. Each partner can focus on their strengths while data flows smoothly between systems.
Mobile-first solutions for field teams
Field teams need quick access to project information from any location. Nearly 100% of construction employees use smartphones for work, making mobile solutions vital to success.
Premier's mobile features let teams:
● Update project status immediately
● Get important documents quickly
● Track equipment and resources
● Submit time cards and reports
● Manage safety protocols
Field teams can work even with poor connectivity. The system keeps data locally and updates automatically when connection returns. Teams stay productive in challenging environments without losing information.
Live GPS tracking and immediate updates from the field give construction managers complete oversight. They can optimize resources and tackle site challenges quickly.
Mobile solutions and back-office systems create continuous information flow. Project managers learn about progress, issues, and resource needs right away. Quick communication leads to faster decisions and fewer delays.
Smart Resource Allocation
AI transforms resource allocation in construction project management. Studies reveal AI-powered systems can improve construction efficiency by 15-20% when resources are deployed more intelligently.
AI-powered scheduling techniques
AI algorithms analyze past project data to make precise scheduling predictions. These systems generate thousands of schedule variations to find the quickest build options. Construction managers who use AI-powered scheduling see major improvements in their project timelines and resource use.
The technology stands out at:
● Predicting delays and bottlenecks
● Optimizing crew assignments
● Calculating exact material needs
● Adjusting schedules live
● Cutting equipment downtime
Live equipment tracking
Construction sites lose about 1,000 pieces of equipment to theft monthly, with recovery rates at just 20%. GPS tracking systems watch valuable assets continuously across job sites.
Premier Construction Software works with IoT sensors to track equipment usage patterns and maintenance needs. This combination helps stop unauthorized use and lowers equipment theft risks. The system logs engine hours and monitors active use periods automatically, which helps managers deploy equipment better.
Automated resource optimization
AI-driven resource optimization handles large amounts of live data to predict demand and spot risks. The system looks at workforce skills, availability, and output to place workers where they add the most value.
Construction companies that use automated resource management see clear benefits. The technology cuts manual data entry errors and gives accurate, live information for better decisions. Weather data helps project managers adjust timelines before delays get pricey.
Smart resource allocation through AI leads to measurable improvements:
● Minimized waste in material ordering and labor scheduling
● Reduced downtime through predictive maintenance
● Enhanced safety with automated monitoring systems
● Improved productivity through optimized scheduling
Premier Construction Software's AI features help managers track resource use across projects live. The platform spots scheduling conflicts and suggests the best resource deployment strategies. This analytical approach helps construction teams stay efficient while cutting operational costs.
Data-Driven Decision Making
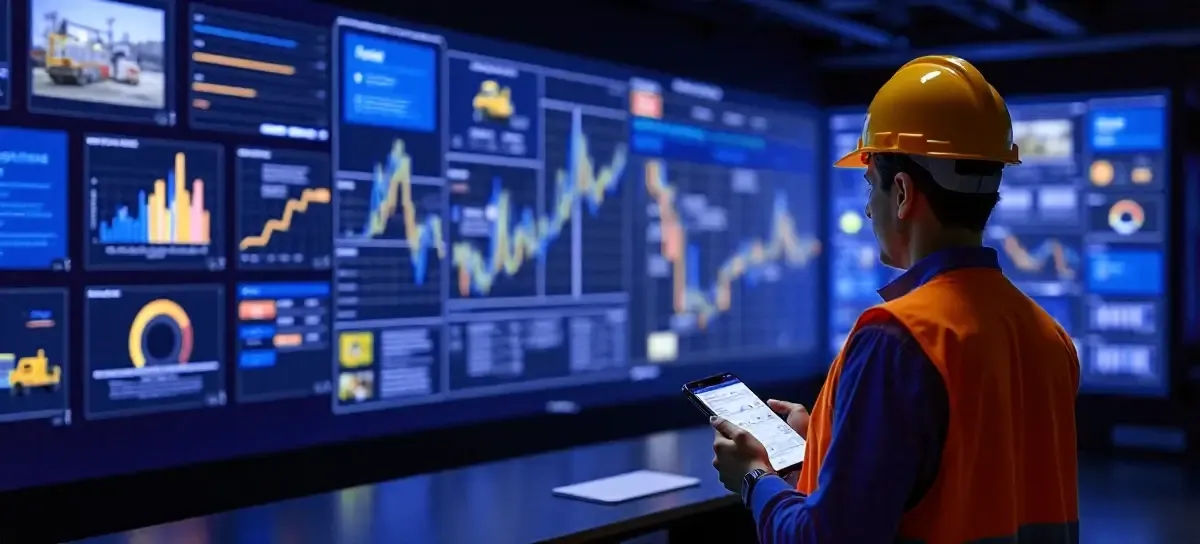
Smart data analysis reshapes construction project management success rates. Companies that use evidence-based strategies achieve a 20% improvement in quality and safety metrics.
Key performance indicators for 2024
Construction managers need to track specific KPIs to get better project outcomes. Premier Construction Software helps teams monitor these vital metrics:
● Project Timeline Adherence
● Resource Utilization Rates
● Task Completion Percentages
● Accounts Receivable Aging
● Cost Tracking Analysis
● Profit Margin Performance
Predictive analytics in construction
Predictive analytics enables construction teams to forecast project outcomes with remarkable precision. The technology uses statistical modeling and machine learning to analyze current and historical data. Construction firms that use predictive analytics spend 25% more time on high-risk issues.
These tools help managers find answers about project bidding, subcontractor performance, and possible challenges. Teams can anticipate delays from weather, material supply, and labor availability by analyzing past project data.
Real-time reporting strategies
Real-time reporting systems provide construction managers instant access to project metrics. Teams can spot issues before they become major problems with this immediate visibility.
Premier Construction Software's reporting capabilities allow managers to:
● Generate accurate job cost forecasts
● Track project expenses against budgets
● Monitor resource usage patterns
● Spot potential risks early
Construction teams reduce project delays and optimize resource allocation with up-to-the-minute data analysis. The system flags deviations from expected quality standards automatically and triggers immediate corrective actions.
Construction teams improve their predictive accuracy by implementing centralized data platforms with standardized input methods. Projects stay on schedule and within budget constraints through this systematic approach to data collection and analysis.
McKinsey & Company reports that predictive analytics and machine learning solutions change how construction firms bid on and execute projects. Companies see improved project outcomes through better risk management and resource optimization when they exploit these tools.
Automated Quality Control
Digital technology is revolutionizing quality control in construction projects. Advanced inspection tools and automated systems are changing how teams maintain standards and track compliance.
Digital inspection protocols
Construction teams that use digital inspection protocols report an 80% reduction in documentation time. These systems use customizable checklists to guide inspectors through critical checkpoints. Digital protocols capture photos, videos, and comments live to create detailed documentation instantly.
Premier Construction Software blends these protocols with automated workflows. The system calculates pass/fail metrics automatically and keeps deficiency logs. This approach helps construction teams identify issues before they become major problems.
Key benefits of digital inspection protocols:
● Immediate data capture and documentation
● Standardized inspection procedures
● Live issue identification
● Photo and video integration
● Automated reporting capabilities
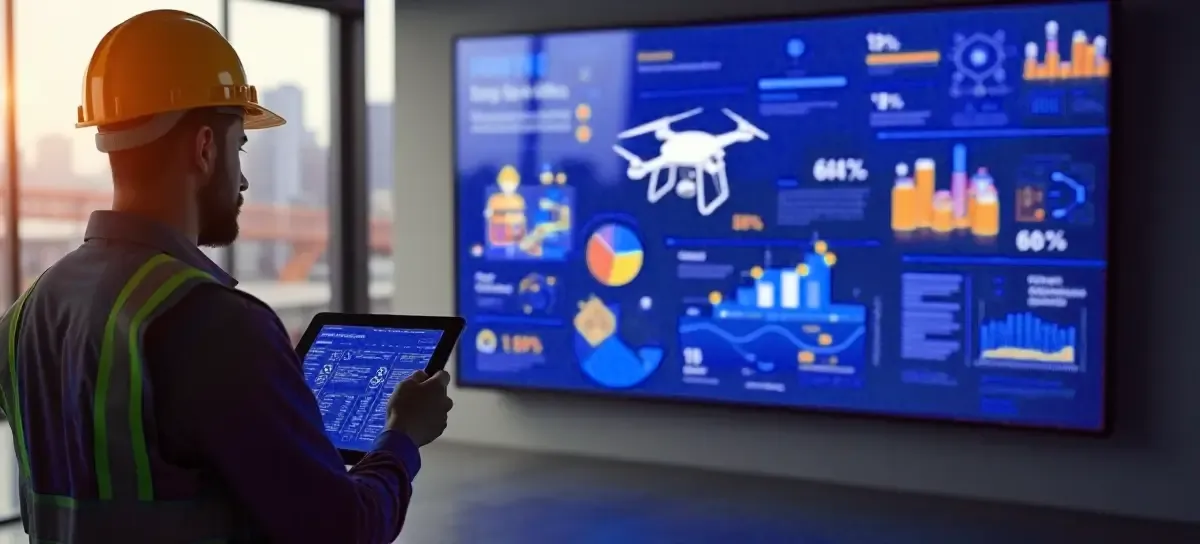
Compliance tracking systems
Modern compliance tracking systems put document management in one place. These platforms cut payment delays by 30% through efficient document processing. Construction managers get instant alerts about compliance status changes to keep projects on schedule.
The system keeps digital records of:
1. Certificates of Insurance
2. Certified payrolls
3. Bond requirements
4. Regulatory documentation
5. Safety compliance records
Quality assurance automation
AI-powered quality assurance systems detect construction defects accurately. These platforms use computer vision and machine learning to analyze visual data live. Construction teams using automated quality control see major improvements in defect detection and resolution speed.
Premier Construction Software's quality control features help teams track issues systematically. The platform identifies deviations from project specifications automatically. This proactive approach helps construction managers fix quality concerns before they affect project timelines.
Digital quality control systems cut administrative workload by 80%. Teams can access inspection data through mobile devices and respond quickly to quality issues. The technology creates accountability through detailed audit trails that document who completed specific tasks and when.
Construction companies using automated quality control systems report better collaboration between field teams and office staff. The technology closes communication gaps through centralized data access. Project managers get immediate updates about quality concerns and can take swift corrective actions.
AI monitoring systems watch construction processes continuously. The technology studies patterns from previous projects to predict potential quality issues. This predictive capability helps teams prevent problems instead of just reacting to them.
Risk Management Through Technology
Technology is changing how construction projects handle risk management through better prediction and prevention systems. Premier Construction Software blends these features to help teams spot and fix problems before they affect project schedules.
Predictive risk assessment tools
AI-powered analytics can spot project risks with amazing accuracy. Construction companies that use predictive analytics catch 75% of potential issues before they become major problems. These systems look at patterns from past data, weather conditions, and resource availability to warn about possible delays.
Premier's risk assessment tools give construction managers the power to:
● Spot supply chain disruptions
● Forecast weather-related delays
● Find potential resource shortages
● Work out financial risk exposure
● Keep track of subcontractor performance
Digital documentation systems
Cloud-based documentation systems make risk management smoother. Teams see a 30% drop in project delays when they can access documents easily. These digital platforms serve as a central hub for all project files and make compliance tracking and risk assessment quicker.
The setup process has these steps:
1. Creating digital document storage
2. Making standard templates
3. Setting up access controls
4. Adding version control
5. Teaching team members
Companies that use cloud systems save about $16,000 yearly per person on time they'd spend looking for information. Teams can focus on managing risks instead of paperwork.
Automated safety monitoring
Smart monitoring systems are changing construction site safety. The industry saw 951 workplace deaths in 2021. This shows why we need better safety solutions. AI-powered monitoring helps prevent accidents by spotting dangers right away.
These systems come with several safety features:
● Smart Wearables: Watch worker health and tell supervisors about problems
● Drone Surveillance: Check sites for dangers before workers arrive
● IoT Sensors: Keep an eye on site conditions and equipment
● Immediate Alerts: Tell managers about safety issues instantly
Teams using automated monitoring see big improvements in safety. AI can learn from past projects to predict safety risks. This helps stop accidents before they happen.
Premier Construction Software combines these safety monitoring tools with project management. The system tracks compliance, creates safety reports, and warns managers about risks. Immediate data analysis helps teams stay safe while keeping projects on track.
The technology watches many risk factors at once. Computer vision systems check construction activities day and night. They find hazards that people might miss. This constant watching makes work safer and reduces accident risks.
Digital systems also help office and field teams talk better. Managers get quick updates about risks so they can act fast. Quick communication stops small issues from growing into big problems.
Conclusion
Technology keeps changing everything in construction project management. AI-powered tools, smart resource allocation, and automated quality control systems create better project outcomes. Companies that accept new ideas about digital solutions get higher success rates with fewer delays.
Premier’s construction management software leads this digital transformation. Their project management platform combines features like up-to-the-minute tracking, automated quality control, and predictive analytics. Construction teams see major improvements in efficiency and risk management when they use these tools.
Construction management's future depends on analytical insights and automated processes. Smart technology helps construction teams avoid mistakes that get pricey, maintain safety standards, and deliver projects on time. Construction managers who follow these seven tips will set their projects up for success in 2024 and beyond.
Latest articles
Trusted by global leaders
Join those who have put their trust in us