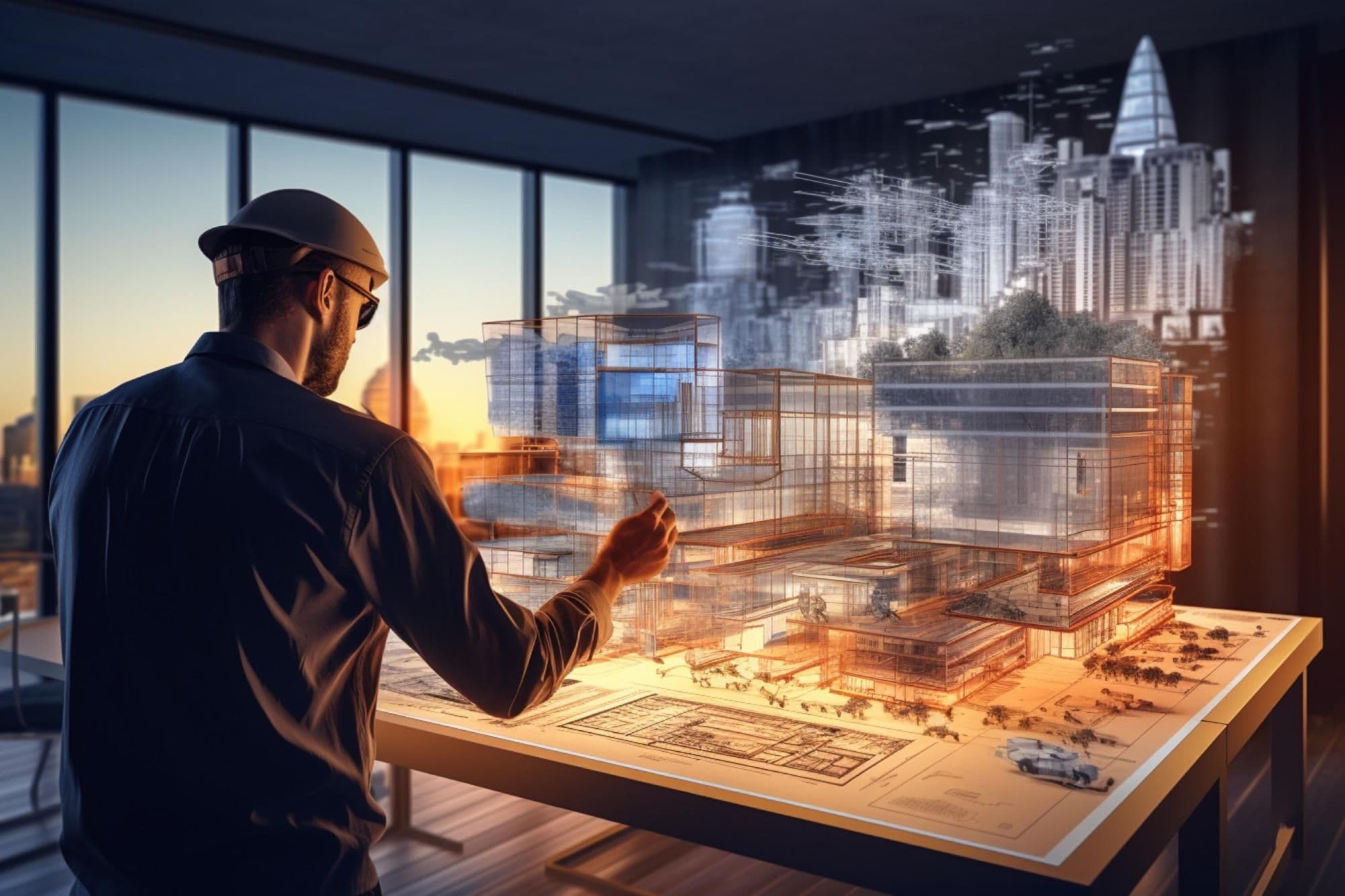
Building Smarter: Your Practical Guide to Construction Data Analytics
This article explains how you can use construction data analysis to improve project outcomes. You'll find practical ways to cut costs, enhance safety, optimize resources, and win more bids through evidence-based decisions
The construction industry fails to use 96% of its generated data. Companies can gain a competitive edge by tapping into data analytics. Poor data management caused the industry to lose $1.84 trillion in 2020 alone.
KPMG research shows that 90% of construction companies will rely on analytics tools to improve planning, reduce errors, and get immediate project updates. About 45% of companies already use simple analytics tools, while another 45% are adopting digital analytics solutions.
This piece explains how you can use construction data analysis to improve project outcomes. You'll find practical ways to cut costs, enhance safety, optimize resources, and win more bids through evidence-based decisions. The content helps both newcomers and experienced users turn raw data into valuable insights.
Solving the Project Delay Puzzle with Analytics
Construction projects often run behind schedule, with about 75% missing deadlines. Project delays typically range from 20% to 40% of the planned duration. Data analytics offers practical ways to tackle this ongoing challenge.
Identifying delay patterns in historical data
Looking at past data shows common reasons why construction projects get delayed. Research shows that longer tasks have more chances of running into trouble. Project teams look at previous performance data to find repeated problems and take steps to prevent them.
Data analysis in construction points to several schedule delay causes:
- Material shortages and supply chain disruptions
- Labor availability fluctuations
- Equipment maintenance gaps
- Weather-related interruptions
- Regulatory compliance delays
Up-to-the-minute data analysis techniques
Modern tracking systems show project status instantly. Teams watch progress through central platforms that combine data from various sources. Top construction project management software includes these tracking features. This helps teams spot possible delays before they disrupt schedules.
Essential parts of progress tracking include:
- Document management systems that serve as single source of truth
- Centralized communication channels
- Task-specific progress monitoring
- Photo documentation with GPS tagging
- Integration with scheduling tools
Up-to-the-minute tracking has cut monthly reporting time from five days to one. This 80% boost in reporting speed lets teams make faster decisions when delays threaten projects.
Predictive scheduling using analytics in construction industry
Predictive analytics reshapes project scheduling by studying patterns in current and past data. Machine learning algorithms watch project information and fine-tune predictions as work moves forward.
AI systems study multiple factors:
- Weather patterns and seasonal effects
- Resource availability trends
- Supply chain dynamics
- Equipment performance data
- Labor productivity metrics
Project managers use these findings to plan ahead. To cite an instance, if data shows certain tasks take longer in specific seasons, teams can adjust their resource planning.
Construction analytics also improves:
- Fleet utilization through IoT sensors
- Just-in-time material delivery
- Crew productivity levels
- Equipment maintenance schedules
- Quality control processes
Case study: Cutting project time by 15% with data insights
A newer study, published in about a 9.6MW data center project shows data analytics' value. The project seemed on track until up-to-the-minute analysis revealed a possible six-week delay.
The team found actual progress at 9% instead of the planned 14%. Using these findings, they created a focused recovery plan:
- Optimized workforce deployment
- Daily site assessments
- Regular stakeholder meetings
- Milestone-based progress tracking
Data-driven controls brought impressive results:
- 40% fewer procurement stage delays
- 60% fewer data-related errors
- 30% better project delivery times
- 50% fewer non-compliance incidents
Teams using predictive analytics get extra benefits:
- Early risk detection
- More accurate resource allocation
- Better communication
- Better quality control
- Faster decision-making
The construction industry loses billions each year through delays. In spite of that, data analytics helps identify, predict, and prevent schedule overruns. Teams can cut project delays and deliver better results by mixing historical analysis, instant tracking, and predictive scheduling.
Stopping Budget Bleeds with Data-Driven Controls
Construction projects struggle with budget issues. About 90% go over budget. Data analytics provides exact solutions by controlling costs systematically.
Cost variance detection systems
Cost variance analysis compares actual spending to planned budgets. This method breaks down costs into specific categories: original bid, bid errors, approved changes, pending changes, and specific problems.
The best construction management software now includes cost variance detection. Teams can watch project finances live. The system alerts teams quickly when costs deviate from plans.
Financial tracking with analytics reveals:
- How accurate bid estimates are
- How change orders affect costs
- Changes in labor costs
- Material price changes
- Equipment cost differences
A USD 20,000 negative cost variance points to budget problems in foundation work. Teams can find why it happens and fix issues before they grow bigger.
Material waste reduction through analytics
Construction creates 40% of global waste. Analytics tools cut this waste by tracking orders and usage precisely. AI systems watch how materials get used and predict what teams will need.
Smart analytics cut material waste by:
- Creating material lists from blueprints automatically
- Checking inventory levels live
- Predicting material needs accurately
- Finding the best times to reorder
- Reducing storage and handling losses
AI tools spot different types of construction waste at collection sites and calculate their weight. This helps teams manage waste better and recycle more.
Video analytics and sensors track materials and spot waste quickly. Teams use this data to buy materials smarter and avoid ordering too much.
BIM makes quantity calculations exact, which stops over-ordering. Teams get detailed digital models to estimate materials and schedule work precisely.
Labor productivity optimization
Labor makes up 15-30% of project costs. Analytics spots productivity patterns and ways to improve. Construction productivity grew just 10% from 2000 to 2022, while the whole economy improved by 50%.
Studies show teams waste 11-15% of field labor costs. Analytics helps save this money through:
- Live productivity tracking
- Better resource planning
- Smarter task scheduling
- Performance analysis
- Matching skills to tasks
Residential construction saw big changes in productivity. Multi-family housing became more efficient from 1993 to 2007 as output grew faster than work hours. Single-family construction productivity dropped through 2019.
Industrial building construction showed the biggest improvements since 2019. Teams made smarter decisions about workers and resources using data.
Labor optimization with analytics brings clear benefits:
- Less idle time
- Lower overtime costs
- Better skill matching
- Faster project completion
- Smarter resource use
Construction companies can save 6-10% on labor costs by managing better. This could save USD 15-25 billion across the industry.
Analytics helps predict and schedule labor needs exactly. Teams track how well resources are used, overtime patterns, and productivity to make smart staffing choices. This approach cuts labor costs while keeping quality high.
Building Safer Sites Through Predictive Analysis
Safety management systems and predictive analytics have cut workplace accidents by 40%. Construction sites now combine analytical insights with active safety measures to keep workers safe.
Leading vs. lagging safety indicators
Safety indicators come in two types. Leading indicators serve as warning signs that predict possible hazards. Past incidents and their effects are measured by lagging indicators.
Leading indicators include:
- Safety training completion rates
- Site inspection frequency
- Equipment maintenance schedules
- Near-miss reports
- Employee feedback surveys
Lagging indicators track historical data points:
- Recorded incidents
- Lost workdays
- Workplace accidents
- Close calls
- Workers' compensation costs
Research covering 47 construction projects showed fewer first-aid injuries at sites with more inspections and toolbox talks. Top construction management software combines both indicator types to create a complete safety monitoring system.
Using construction data analysis to spot safety risks
Predictive modeling catches potential accidents with 87% accuracy. Construction analytics looks at patterns across multiple data sources to find risk factors. Raw data turns into applicable safety information through this systematic approach.
AI-powered systems analyze various elements:
- Historical incident data
- Environmental conditions
- Worker behavior patterns
- Equipment performance metrics
- Site-specific hazards
Ground applications prove this works. Turner Construction cut fall incidents by tracking worker movements with IoT wearables. Skanska found high-risk electrical situations by studying previous incident data. Bechtel reduced heat stress risks by mixing task schedules with worker health data.
Wearable technology and safety analytics integration
Smart wearables track vital signs and environmental conditions as they happen. These devices monitor heart rates, body temperatures, and physical activity levels. Construction teams get instant alerts about possible health risks or unsafe conditions.
Wearable safety breakthroughs include:
- Smart boots with GPS and environmental sensors
- Augmented reality safety glasses
- IoT-enabled hard hats
- Exoskeletons to reduce physical strain
Smart helmets spot dangers through proximity warning systems. Exoskeletons help painters and welders work better by reducing shoulder discomfort. Wireless mesh networks connect these technologies and enable up-to-the-minute monitoring and analytics.
Safety AI spots visible risks based on OSHA standards automatically. Beta testing revealed an 89% drop in unsafe conditions within three weeks. The system analyzes data across projects and provides company-wide safety trends for active risk management.
Construction firms using analytics report:
- Faster response times to hazard reports
- Improved compliance tracking
- Better risk prediction
- Better resource allocation
- Reduced incident rates
Predictive safety analytics studies both safe and risky behaviors. This balanced approach helps teams find successful safety practices and potential hazards. Teams use these insights to strengthen preventive measures and build a safety-first culture.
Analytics-based safety decisions bring clear benefits. Companies see fewer workplace accidents, lower costs, and better safety performance. Most importantly, this analytical approach prevents incidents before they happen and saves lives.
Winning More Bids with Data-Backed Estimates
Smart construction companies win more bids by analyzing their past project data. Research shows companies making evidence-based decisions improved their project outcomes by 89%. Raw project information becomes winning bid strategies through this methodical approach.
Competitive analysis using historical project data
Past project data shapes winning bid strategies. Companies learn which opportunities bring profit and which ones carry risk by analyzing their previous outcomes. Customer relationship management (CRM) tools reveal valuable patterns in project success rates.
Key data points for competitive analysis include:
- Worker certification status
- Equipment utilization rates
- Material costs
- Direct labor expenses
- Project completion times
Leading construction management software blends these data points to create detailed bid analysis tools. The system measures past performance to predict future project success.
Construction cost databases hold essential project details throughout the preconstruction phase. Teams make better decisions with this data instead of relying on experience alone. Companies that use this information well have a huge advantage, since 95% of construction data remains unused.
Accuracy improvements through analytics
Analytics makes bids more precise through detailed cost analysis. Construction financial management software looks at thousands of unit line items, which cost engineers verify. This helps reduce estimation errors and boost profit margins.
Labor costs just need special attention since they make up 40% of project budgets. Analytics tools break down these expenses into:
- Preparation time
- Direct work hours
- Non-productive periods
Cloud platforms give stakeholders up-to-the-minute data analysis. Multiple estimators can cooperate better because everything stays transparent, which leads to more accurate bids.
Construction firms using analytics report:
- 20% reduction in estimation errors
- 15% improvement in bid accuracy
- 30% increase in successful project outcomes
Client confidence factors in data-supported proposals
Data-backed estimates build trust through transparency. Companies show their expertise with detailed analytics supporting their proposals. Project owners want more information early in the project lifecycle.
Up-to-the-minute dashboards show proof of numbers, letting teams:
- Present clear cost breakdowns
- Measure against similar projects
- Track project profitability
- Identify efficiency improvements
- Offer better solutions to owners
Construction estimating becomes more profitable with real project data support. Contractors gain future bidding advantages by collecting accurate project information.
Analytics tools help predict potential risks. Teams can add appropriate contingencies without overpricing their bids. Construction management software makes this efficient by tracking cost history throughout project lifecycles.
Companies using analytics in their bidding process see:
- Higher win rates on competitive projects
- Increased client satisfaction scores
- Better long-term client relationships
- Improved project predictability
Evidence-based decisions strengthen contractor-client relationships by promoting trust and transparency. Teams defend their estimates with dashboards showing concrete evidence. Clients understand the value behind each bid better this way.
Construction companies save time through automated data analysis. Teams focus on strategic decisions instead of manual calculations. Analytics helps companies avoid underbidding or overbidding - two critical risks in construction estimation.
Optimizing Equipment and Resource Allocation
Leaders in the construction industry spend 11.5 hours weekly analyzing data and conducting research. Construction companies use advanced analytics to optimize their equipment management and resource allocation.
Fleet utilization analytics
Fleet analytics turns equipment data into practical insights. Teams track odometer readings and operating hours to plan maintenance schedules. Equipment sensors connect to telematics devices that provide live data about:
- Engine temperatures
- Fluid levels
- Equipment alerts
- Runtime statistics
- Location tracking
The best construction management software merges these data feeds into single dashboards. Managers can spot usage patterns and make smart choices about where to deploy equipment. Live tracking lets supervisors know about delays so they can move idle machines where they're needed most.
These dashboards show key metrics:
- Fleet usage percentage
- Runtime by asset type
- Asset usage history
- Maintenance schedules
- Equipment downtime
Companies using fleet analytics see a 30% boost in equipment efficiency. This technology helps prevent breakdowns with planned maintenance.
Just-in-time material delivery systems
Just-in-time (JIT) delivery cuts excess inventory and waste. Materials show up right when workers need them. This method offers several advantages:
- Lower storage costs
- Less material damage
- Better site safety
- Better cash flow
- More space on site
Construction teams save money with JIT systems. They don't need to order in bulk, which reduces waste. Materials go straight from delivery trucks to installation areas, which cuts handling costs and damage risks.
Teams hold daily meetings to coordinate deliveries. Construction management software makes this easier by handling schedules and supplier coordination automatically.
Crew productivity optimization through construction technology data analytics
Data analytics helps teams make faster decisions by turning raw numbers into useful information. Today's construction sites collect data from many sources:
- Schedules
- Accounting systems
- Project management platforms
- Workforce metrics
- Equipment sensors
AI-powered systems find patterns in construction data that humans might miss. Project managers can see progress, equipment status, and safety conditions instantly.
Construction crew software handles essential tasks:
- Work scheduling
- Progress tracking
- Team communications
- Performance monitoring
- Resource allocation
These digital tools cut monthly reporting from five days to one. Teams can focus on planning instead of processing data. The software analyzes standard data sets automatically, which gives teams more time to make decisions.
Analytics helps construction firms reduce costs by tracking:
- Rental expenses
- Fuel use
- Safety incidents
- Service events
- Fleet utilization
Companies save valuable time through automated analysis. Teams can concentrate on strategic planning rather than basic calculations. Analytics helps prevent resource bottlenecks and boosts productivity across job sites.
Weather-Proofing Projects with Predictive Tools
Weather costs construction projects billions of dollars each year due to delays and disruptions. Modern weather intelligence systems help predict and prevent these setbacks through evidence-based planning.
Weather impact modeling for schedules
Weather modeling turns historical data into practical insights. Construction planners get into 20 years of weather patterns to learn about possible disruptions. This helps them schedule critical activities when conditions are best.
Leading construction management software smoothly combines weather data with project timelines. The system looks at weather patterns to identify:
- Temperature limits for installing materials
- Wind speed restrictions for crane operations
- Rain forecasts for concrete work
- Seasonal patterns that affect productivity
Records show weather caused 17,350 schedule disruptions last year. Construction teams can spot weather risks early through predictive modeling. The National Oceanic and Atmospheric Administration (NOAA) gives detailed climate data to help calculate weather days for each location.
Mitigation strategies based on data patterns
Evidence-based weather planning needs clear criteria. Construction teams set specific limits for:
- Rain amounts that stop work
- Temperature ranges for installing materials
- Wind speeds that restrict equipment use
Weather intelligence platforms alert teams about severe conditions automatically. Teams get enough time to:
- Secure materials and equipment
- Change work schedules ahead of time
- Protect the site
- Plan indoor work
- Update delivery times
Studies show weather delays affect 45% of construction projects yearly. Smart mitigation strategies reduce weather downtime by 20%. Construction management software makes this easier with automated weather tracking and response plans.
Integration with Premier construction management software for weather planning
Premier's platform combines weather data with project scheduling. The system flags risky weather periods and suggests schedule changes. Teams can stay productive even in challenging conditions.
Weather analytics brings real results:
- Weather delays down 51% in Gulf Coast projects
- Asphalt work scheduling improved by 96%
- Equipment damage decreased by 30%
Remote work options help teams stay resilient during bad weather. Project management continues through digital platforms when outdoor work stops. This flexibility reduces financial losses from weather delays.
Construction companies now employ climate modeling to build project resilience. Advanced analytics study:
- Historical weather patterns
- Seasonal changes
- Regional climate trends
- Storm frequency
- Temperature extremes
Weather platforms process this data to create site-specific forecasts. These accurate predictions let construction teams:
- Schedule temperature-sensitive work effectively
- Plan deliveries around weather events
- Assign crews based on conditions
- Keep equipment safe
- Maintain worker safety
The technology studies how weather affects different aspects of construction. AI systems analyze patterns to predict how specific conditions affect various activities. Teams can develop targeted strategies with this detailed information.
Construction companies save money by using weather analytics. This technology prevents costly delays while protecting materials, equipment, and workers. Evidence-based weather planning brings certainty to what used to be an unpredictable part of construction management.
Measuring and Improving Quality Outcomes
Quality control is the foundation of successful construction projects. Many firms find it hard to set up good quality management systems. Data analytics provides a solution that gives useful insights to improve results.
Construction quality metrics do more than just pass or fail assessments. They show a detailed view of how projects perform. Key performance indicators (KPIs) show how well a business meets its goals. Financial targets such as cost, cash flow, and profit are the most common construction KPIs.
Quality metrics that matter
Good quality control begins with picking the right metrics. Here are some key indicators:
- Defects Rate: This metric shows how many defects occur compared to completed work. The calculation is:
Defects Rate (%) = (Number of Defects / Total Work Completed) × 100
Lower defect rates are linked to happier clients and more referrals. - Rework Rate: This shows how much work needs fixing or redoing. Here's how to calculate it:
Rework Rate (%) = (Amount of Rework / Total Work Completed) × 100
High rework rates usually mean more costs and delays. - Schedule Adherence: This shows if a project stays on its planned timeline. The formula is:
Schedule Adherence (%) = (Actual Progress - Planned Progress) × 100 - Safety Incidents Rate: This tracks how often safety incidents happen. Here's the calculation:
Safety Incidents Rate (%) = (Number of Safety Incidents / Total Work Hours) × 100 - Client Satisfaction Index: This measures how happy clients are through surveys and feedback.
- Labor Productivity: This shows how efficient the workforce is. The formula is:
Labor Productivity (%) = (Actual Output / Planned Output) × 100
These metrics paint a clear picture of project health and help teams learn about areas to improve.
Defect pattern recognition
Finding patterns in defects helps improve construction quality. Smart analytics tools look at past data to spot common issues. This helps stop problems before they start.
AI systems can spot different types of defects:
- Structural defects (cracks, settlement issues)
- Moisture-related problems (dampness, mold growth)
- Finishing defects (paint deterioration, material spalling)
- Installation errors (misaligned components, improper connections)
Recent studies show AI's power in finding defects. A newer study, published by AI tools found building defects with 89% accuracy. The system looked at data from many projects to show safety trends.
Dampness causes many building defects. It leads to:
- Mold and fungal growth
- Material spalling and blistering
- Cracking and crazing
- Steel and iron rusting
- Decay from microorganisms
Construction teams can fix issues early by spotting these patterns. This cuts down rework and makes projects better.
Continuous improvement systems using construction industry data analytics
Data analytics makes construction better. It turns project data into useful insights. Companies use this approach to make their work better.
Here's what makes data-driven improvement work:
- Standardized reporting: Using the same format for all project data makes analysis easier. Teams can compare how different sites perform.
- Automated analysis: AI tools process big amounts of data fast. This gives teams more time to make smart decisions.
- Flexible visualization: Custom dashboards show important data clearly. Teams can focus on what matters most for their projects.
- Up-to-the-minute data analysis: Quick access to project data helps solve problems fast. Small issues don't become big problems.
- Predictive modeling: Smart analytics tools can spot quality issues before they happen. Teams can use resources better this way.
The best construction management software blends these features to manage quality well. Teams get instant data insights to make better choices throughout the project.
Data-driven quality management brings clear benefits:
- 20% fewer estimation errors
- 15% better bid accuracy
- 30% more successful projects
Companies that use data analytics also have happier clients and better long-term relationships.
Construction companies can use data to always get better. Looking at metrics regularly helps improve processes and find best practices. This approach keeps companies competitive as the industry changes.
Data analytics helps construction firms transform quality management. Teams make smarter choices, reduce mistakes, and deliver better results with these tools. Data-driven quality control will become more significant as the industry grows.
Conclusion
Construction analytics transforms raw information into powerful business benefits. The right management software helps you convert 96% of unused data into practical insights that lead to better project results.
Your construction data has stories to tell. Analytics shows patterns in delays, costs, and safety incidents. These findings help make smarter decisions about resources, weather planning, and quality control.
The results are clear. Construction firms that use analytics show:
- 40% fewer workplace accidents
- 20% reduction in estimation errors
- 30% improvement in project delivery times
- 51% decrease in weather-related delays
Evidence-based construction management reduces costs and optimizes efficiency. Teams make informed decisions instead of searching for information. Premier's construction management platform simplifies this process by putting vital project data within reach.
Companies that adopt analytics will lead the future of construction. Your data experience can begin today. Better data management creates most important improvements in project outcomes. Smart data use paves the way to your next successful project.
Note that each data point gives you a chance to build better, faster, and safer. Your competitive edge depends on taking control of your construction data.
Latest articles
Trusted by global leaders
Join those who have put their trust in us