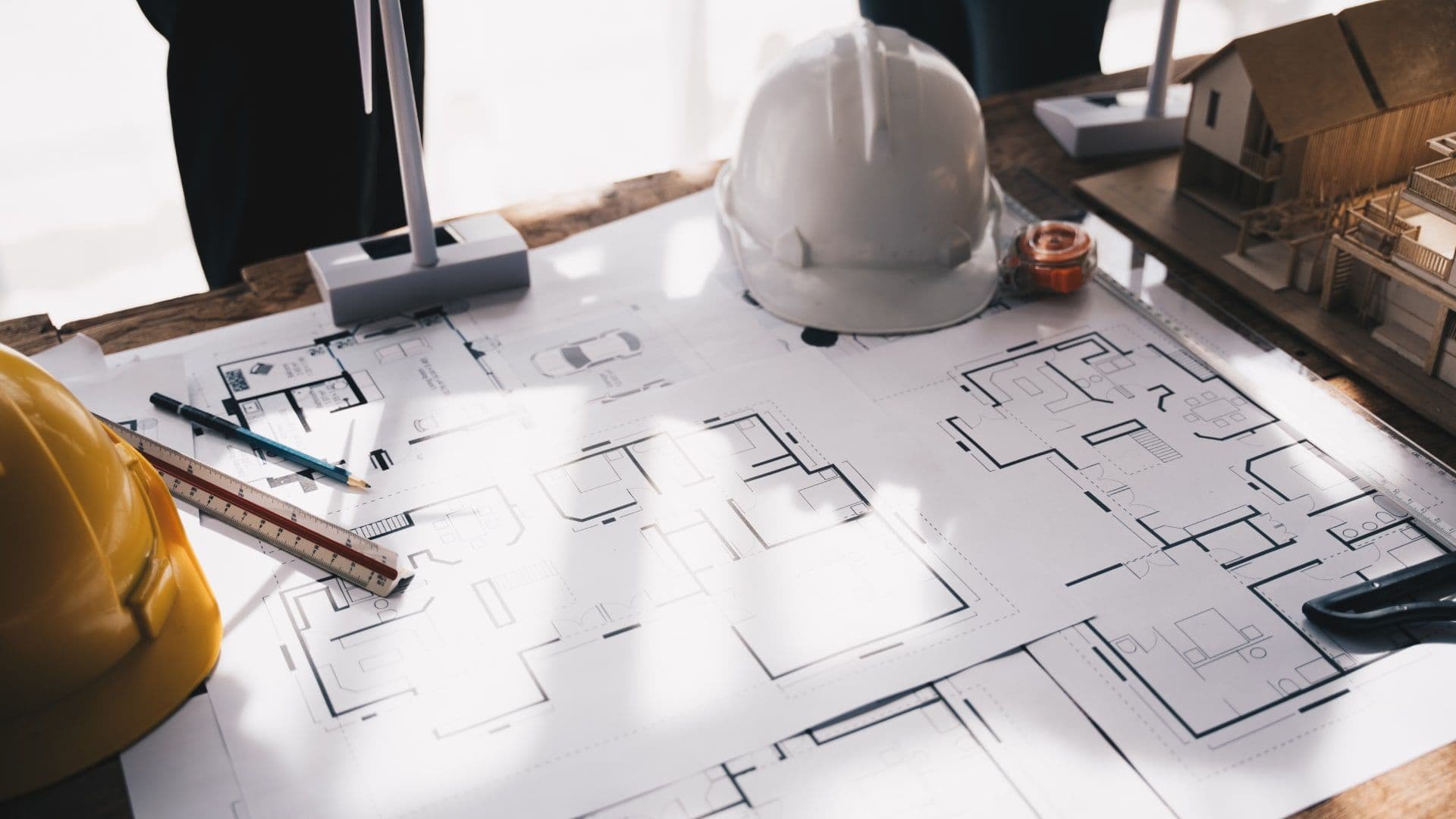
As-Built vs Construction Drawings: What's the Real Difference?
The global drafting services market now exceeds $5 billion. This milestone emphasizes how as-built drawings and construction drawings play crucial roles in modern building projects. These technical documents form the foundation of successful construction and serve unique purposes throughout the project lifecycle.
Construction drawings contain detailed layouts and specifications. They include dimensions, materials, and electrical systems that guide the building process. The original plans establish the groundwork, while as-built drawings serve a different purpose by capturing the real-life state of the completed project.
Proper drawing documentation matters more than simple record-keeping. Clients use as-built drawings to review completed projects and verify installations, especially when you have emergency services and utilities. A clear documented history makes future maintenance and operations easier.
Construction professionals need efficient drawing management tools to handle these vital documents. Premier Construction Software provides these capabilities effectively. Drawing misunderstandings can get pricey and cause errors that affect project timelines and budgets significantly.
What Are As-Built Drawings in Construction
Simple definition and purpose
As-built drawings are revised documents that contractors submit after completing a project. These drawings capture the exact specifications and conditions of the finished project and document all modifications made during construction.
Contractors create these drawings to show changes in specifications, working drawings, and field adjustments throughout the construction process. The drawings display precise dimensions, geometry, and locations of all completed work elements. They help teams compare the original design with the final product.
Premier Construction Software's drawing management features help contractors track these modifications systematically. All versions stay in one available location.
Key components
As-built drawings have these vital elements:
- Building layout and structure documentation, including floor plans, elevations, and structural components
- Design features covering doors, windows, walls, stairs, and lighting
- Mechanical systems information for HVAC, plumbing, and electrical installations
- Utility documentation showing water, sewage, gas, and electrical connections
- Interior finish specifications detailing materials used
These drawings must record specific details about modifications, such as dates of changes, material alterations, dimension updates, and installation adjustments. They also document predicted obstacles encountered during construction and their solutions.
The drawings need clear labels and descriptions instead of vague phrases like "similar" or "equal to". They should match the scale of original drawings whenever possible. Written notes, photographs, and related shop drawings often support the documentation.
As-built surveys are the foundations of creating these drawings. These surveys track the structure's and surrounding land's changes throughout each construction phase. Teams can maintain accurate as-built documentation by recording variations from original plans consistently during the project.
Construction Drawings Explained
Construction drawings are the foundations of every building project. They serve as detailed visual guides that turn architectural concepts into buildable structures. These drawings outline the project's scope, timeline, and resources and act as contract references between stakeholders.
Core elements
Construction drawings have several key components:
- Floor plans and elevations showing spatial layouts
- Structural details depicting load-bearing elements
- MEP (Mechanical, Electrical, Plumbing) systems layouts
- Site plans showing building placement
- Material specifications and schedules
Premier Construction Software provides digital tools to organize these elements in a way that lets teams access and modify plans live.
When they're created
Construction drawings go through different development stages to reach their final form. Architects start by creating schematic designs that show simple layouts and proportions. The design team then refines these concepts through detailed development.
The construction document phase creates the final set needed for approvals and bids. Structural engineers work on stability elements at this stage, and MEP engineers add infrastructure systems after that. Civil engineers complete the package by adding site plans and landscape architecture.
Each drawing works as a legal document that shows agreements between architects, engineers, and clients. These documents help get necessary permits because reviewing authorities use them to check safety and zoning compliance. Projects might face delays, fines, or required design changes if they don't comply.
Digital drawing management platforms have made it easier to share and update plans. Changes to construction drawings will still happen throughout projects because of design revisions, material substitutions, or field adjustments. Project managers send updated drawings through formal processes and mark them with revision codes and dates to track changes.
The drawings help different trades communicate on site. They give precise specifications that prevent misunderstandings and reduce errors. These documents also help with resource allocation, scheduling, and budget planning by providing detailed material lists.
Key Differences Between As-Built and Construction Drawings
The basic differences between as-built and construction drawings help teams manage projects and documentation better. These differences affect how construction teams handle project documentation at each stage.
Creation timeline
Construction drawings are the first step in any building project, created before ground is broken. These original blueprints guide the construction process and set clear expectations. As-built drawings change throughout the project, and teams finalize them after completion.
Premier Construction Software's drawing management system tracks these changes over time. Teams can update drawings as the construction moves forward.
Level of detail
These drawing types differ by a lot in their detail level. Construction drawings show conceptual elements but might miss real-life challenges that pop up during building. As-built drawings capture exact details, including:
- Precise measurements and dimensions
- Actual materials used
- Field modifications and adjustments
- Solutions to unexpected obstacles
- Final equipment locations
As-built drawings need higher accuracy standards because they document the actual state instead of planned specs. Every change goes into these drawings, from small tweaks to major design shifts.
Purpose and use
Construction drawings work as roadmaps for builders and contractors to show the original project vision. As-built drawings serve different purposes:
They help facility managers by providing accurate reference points for maintenance and repairs. Building owners use these documents to understand their property's exact details.
These drawings help verify if contractors met their obligations and followed project requirements. Local building authorities check these documents during final inspections.
Future renovations or expansions become easier with these drawings. They show exact locations of utilities, structural elements, and building systems, which removes any guesswork.
Premier construction management software boosts drawing management with immediate updates and revisions during construction phases. This digital approach makes it easier to move from construction drawings to final as-built documentation.
Digital Tools for Drawing Management
Digital solutions have revolutionized traditional drawing management practices in construction. Premier Construction Software is pioneering this change with specialized tools for both as-built and construction drawing management.
Premier Construction Software features
Premier's drawing management platform combines complete markup tools with advanced storage capabilities. The software lets users:
- Make detailed annotations and adjust drawings
- Apply professional stamps and signatures
- Attach photos and files directly to drawings
- Track changes through chat discussions
- Access unlimited storage for all common file types
Users can locate specific sheets instantly with the platform's advanced search functionality. The software connects drawings with project elements like documentation, RFIs, submittals, change orders, and daily logs.
Benefits of digital drawing management
Digital drawing management cuts costs significantly. A Texas airport project saved USD 1.00 million by switching from traditional blueprints to digital drawings. Traditional blueprint sets cost USD 23000.00, plus extra expenses for multiple versions and reprints.
Multiple stakeholders can work on drawings simultaneously with the software's collaboration features. Architects, engineers, and subcontractors can join the planning process, which reduces errors and minimizes rework.
Premier's cloud-based platform eliminates data silos through uninterrupted document integration. Teams can access drawing sets from any location, which improves field operations and speeds up decision-making.
Digital tools have simplified version control and drawing validation. Project teams track modifications systematically and store all versions in one location with clear audit trails of changes. This approach reduces confusion and speeds up project timelines.
The platform does more than just simple storage. The complete connection between drawings and project management components creates a unified system where teams quickly find related documents or communications.
Common Problems with As-Built Drawings
Construction teams face ongoing challenges when they try to maintain accurate as-built drawings. Research shows about 30% of as-built drawings have errors or remain incomplete.
Accuracy issues
Construction teams often fail to document field changes and revisions properly. The busy environment of construction sites makes it hard to keep precise records. Premier Construction Software's drawing management tools help track these changes, but many teams still use outdated data collection methods.
Drawing accuracy suffers most from changes during construction. Field teams often miss modifications that come from:
- Design alterations and client requests
- Unforeseen site conditions
- Material substitutions
- Emergency fixes
Missing information
Poor coordination between teams of all sizes creates gaps in communication. Field changes don't reach the documentation team quickly enough. This creates differences between actual construction and recorded details. Junior staff members or interns who lack experience often handle as-built documentation.
Project completion deadlines force teams to rush their submissions. Teams have less time to verify and check quality. Digital tools exist for immediate updates, but contractors often wait until the project ends to document changes.
Storage challenges
Construction teams don't deal very well with data management. As-built drawings generate more information as the project progresses. Old storage methods make it hard to access data and risk losing it.
Teams still use manual measurements and paper-based systems. These old practices make it difficult to:
- Track drawing versions
- Share updates across teams
- Maintain backup copies
- Access information quickly
Premier Construction Software solves these storage problems with cloud-based solutions. Notwithstanding that, many construction teams have trouble organizing and protecting their drawing data.
The core team and design staff often get confused during the handover process. Critical information gets lost without clear protocols. Some contractors submit contract drawings as as-builts without marking changes because they don't understand requirements or lack motivation.
Field teams sometimes hide unauthorized changes. They worry about penalties or extra work requirements. While this might help in the short term, it creates problems for future maintenance and renovations.
How to Create Better As-Built Drawings
A systematic approach and attention to detail are essential to create accurate as-built drawings. Premier Construction Software makes this process easier with digital tools that support live updates and shared verification.
Step-by-step process
The design team holds main responsibility for creating and managing final as-built drawings. Teams start by collecting all information about construction changes.
- Reference Original Plans: Start with the original construction drawings as your base. Premier Construction Software works with many file formats to import existing designs.
- Track Changes: Record modifications throughout construction and add dates next to changes. Changes should cover:
- Material substitutions
- Location changes
- Sizing alterations
- Utility modifications
- Update Continuously: Revise drawings weekly or monthly rather than waiting until the end. This helps catch all changes and optimizes the process.
- Add Supporting Details: Put in shop drawings, appendices, and clear descriptions you might need later. Cross out old information but keep original values visible.
- Organize Documentation: Digital platforms help store changes in order. Premier Construction Software gives you annotation tools and dimensioning features for exact measurements.
Quality checks
The owner's team and design team should check final as-built drawings against change orders, RFIs, and submittals separately. This two-step verification makes the drawings more accurate.
Building owners often create specific checklists to verify drawings. These checklists usually look at:
- Safety systems documentation
- Mechanical system details
- Hazardous materials information
- Equipment specifications
Regular Owner-Architect-Contractor (OAC) meetings help verify drawing accuracy. Teams can approve changes and check documentation together in these meetings.
Local building authorities perform inspections that serve as extra verification points. General contractor inspections and the owner's punch list walkthroughs during closeout also help confirm drawing accuracy.
Premier Construction Software improves quality control with live collaboration and version tracking features. Teams can attach photos directly to drawings to visually verify changes.
Utilities should share detailed product requirements before starting work. This covers approved materials, work order details, and compliance rules. Digital platforms flag potential problems right away so field crews can fix issues quickly.
Real Cost Impact of Poor Drawing Management
Construction projects lose money due to poor drawing management. A newer study, published in shows that wrong documentation leads to 55% of all rework in construction projects.
Direct costs
Bad drawing management hits project finances immediately. Projects typically lose 15% of their budget because teams don't manage documents well. Premier Construction Software's drawing management platform cuts these costs through centralized document control.
Field teams run into expensive problems with outdated drawings. These include:
- Material waste from incorrect installations
- Labor costs for rework and corrections
- Equipment rental extensions
- Project delay penalties
- Additional administrative expenses
A construction company in the UK lost £95,000 on just one project because of drawing mismanagement. The loss broke down to £50,000 in rework costs, £20,000 in delay penalties, and £25,000 in combined labor and material waste.
Hidden expenses
Drawing management problems create costs you can't see right away. Teams waste precious time looking for the right document versions. Field crews often stop work while they wait for updated drawings. This disrupts project schedules and resource planning.
Underground utility strikes add another hidden cost. Research shows that damage to underground utilities adds between USD 50-100 billion in unnecessary costs to the US economy. Singapore's construction industry faced similar problems - wrong as-built records led to bad decisions, slow planning, and more legal issues.
Premier Construction Software's digital platform solves these problems through immediate updates and version control. This approach cuts confusion and speeds up project timelines.
Long-term implications
Money problems don't stop at the project's end. Bad documentation makes future maintenance harder. Building owners face bigger expenses because:
Stakeholders struggle to work together efficiently. Teams need to gather information repeatedly without proper documentation. Worker safety risks go up without accurate facility information.
Research links damage to critical lifelines with weak infrastructure resilience. The United States spent USD 1.5 billion in 2016 on public costs tied to buried services' excavation losses.
Poor as-built drawings often cause extra work, conflicts, and design changes. These problems hurt productivity and drive up operational costs as teams keep checking existing utility assets.
Premier Construction Software's drawing management features help avoid these long-term problems. The platform keeps accurate records throughout the project's life, which reduces future complications and costs.
Industry Standards and Compliance
Construction industry standards define how as-built and construction drawings must be documented. The American Institute of Architects (AIA) has established basic guidelines that control drawing preparation and submission standards.
Required documentation
Premier Construction Software's digital drawing management platform works in line with AIA documentation standards. The software supports these required document types:
- Contract drawings and specifications
- Revision records with delta triangles
- Working hardcopy drawing sets
- Final CAD drawings
- Project inspection cards
- Verified reports
Construction teams should keep at least one working hardcopy drawing set at the site. The contractor must mark all revisions clearly and show associated views, sections, and details. Premier Construction Software makes this task easier with digital annotation tools.
Teams in the field update working drawings every week. Clear handwritten text and proper deletion marks are essential for these updates. The cover sheet must display "RECORD DRAWINGS / AS-BUILT CONDITIONS" along with contractor details and contact numbers.
Legal considerations
As-built drawings serve as legally binding documents. These drawings prove that contractors have met their obligations to owners and authorities with jurisdiction. Local building authorities usually need as-built documentation before they issue occupancy permits.
AIA contract standards spell out who should prepare drawings. Contractors might face legal risks if final designs don't match original plans. Record drawings are more reliable than as-built drawings because architects screen and approve them.
Construction contracts should address how drawings comply with local, state, and federal regulations. These agreements list who gets permits and meets legal requirements. Premier Construction Software helps teams track these tasks through its complete document management system.
Building owners rely on accurate as-built drawings for several legal purposes. These include:
Opening businesses or securing tenants comes first. Property sales and renovations follow next. Insurance claims and legal disputes round out the list.
Quality assurance plays a key role during commissioning. Many owners check drawing accuracy as part of their commissioning process. Requirements vary based on delivery timing, equipment location accuracy, and system distribution details.
Licensed surveyors or engineers must create certain as-built drawings. These professionals write letters that confirm plan information or note any changes. Field conditions that don't match approved plans need detailed documentation, especially for drainage, grades, and floor elevations.
New laws or regulations after contract signing create special challenges. Projects without specific contract clauses about regulatory changes often face disputes over costs and schedules. Smart contracts include provisions that cover how regulatory updates affect project execution.
Comparison Table
Aspect | Construction Drawings | As-Built Drawings |
---|---|---|
Creation Timing | Created before construction begins | Developed during construction, finalized after completion |
Main Goal | Guide construction process and get permits | Document actual built conditions and support future maintenance |
Level of Detail | Shows planned specifications and conceptual elements | Captures exact measurements and ground modifications |
Key Components | • Floor plans and elevations • Structural details • MEP systems layouts • Site plans • Material specifications | • Building layout documentation • Design features • Mechanical systems info • Utility documentation • Interior finish specifications |
Accuracy Requirements | Based on original design concepts | Must reflect exact final conditions with precise measurements |
Legal Status | Contract reference between stakeholders | Verification tool for contractor's obligations |
Main Users | Builders and contractors during construction | Facility managers, building owners, maintenance teams |
Common Problems | Design revisions and material substitutions | • Missing information • Accuracy problems • Poor documentation of field changes |
Storage Method | Digital management through platforms like Premier Construction Software | Digital storage with cloud backup and version control |
Update Frequency | Updated through formal revision processes | Requires continuous updates throughout construction |
Conclusion
Modern building projects rely on two key drawing types. Construction drawings show the original plans and specs. As-built drawings capture the actual conditions after work completion. This difference plays a crucial role in project success and facility management.
The digital world has changed how teams handle drawings. Premier Construction Software's drawing management platform helps teams track changes and maintain accurate docs. Teams can also cut down on errors that get pricey. Their cloud system solves common headaches like version control and team communication gaps.
Latest articles
Trusted by global leaders
Join those who have put their trust in us